Market Trends of United States Maintenance, Repair, And Operations (MRO) Industry
Manufacturing (Industrial MRO) Accounts for the Largest Share
- The adoption of industrial MRO equipment in the manufacturing industry in the country has been impacted by various driving factors, which include the surging demand to reduce cost, ramping market maturity, cyclical fluctuations in new equipment sales, as well as the growing need to enhance product quality. With enterprises in the manufacturing sector continuously looking forward to achieving large profit margins, they have been looking to increase return on net assets (RONA).
- Next to a safety or environmental mishap, unscheduled or unplanned downtime has emerged as one of the costliest events at any manufacturing plant. According to Forbes, an average manufacturer confronts 800 hours of equipment downtime per year, which turns out to be more than 15 hours per week. That downtime arrives at a cost, and it’s quite hefty. For instance, the average automotive manufacturer loses USD 22,000 per minute when the manufacturing line stops, and that swiftly adds up. Collectively, unplanned downtime costs industrial manufacturers as much as USD 50 billion a year.
- Furthermore, manufacturers in the country have been looking towards optimizing their processes to reduce their overall energy consumption in adherence to government regulations. As part of President Biden’s Investing in America agenda, the US Department of Energy (DOE) announced up to USD 6 billion for 33 projects across more than 20 states to decarbonize energy-intensive industries, reduce industrial greenhouse gas emissions, support good-paying union jobs, revitalize industrial communities, and strengthen the nation’s manufacturing competitiveness.
- The rising demand for industrial MRO services and solutions as the industrial segment has been the second largest energy consumer in the country, as per EIA. In the process, manufacturers have been conducting lifecycle assessments of their products and incorporating the required MRO equipment to practice lean manufacturing.
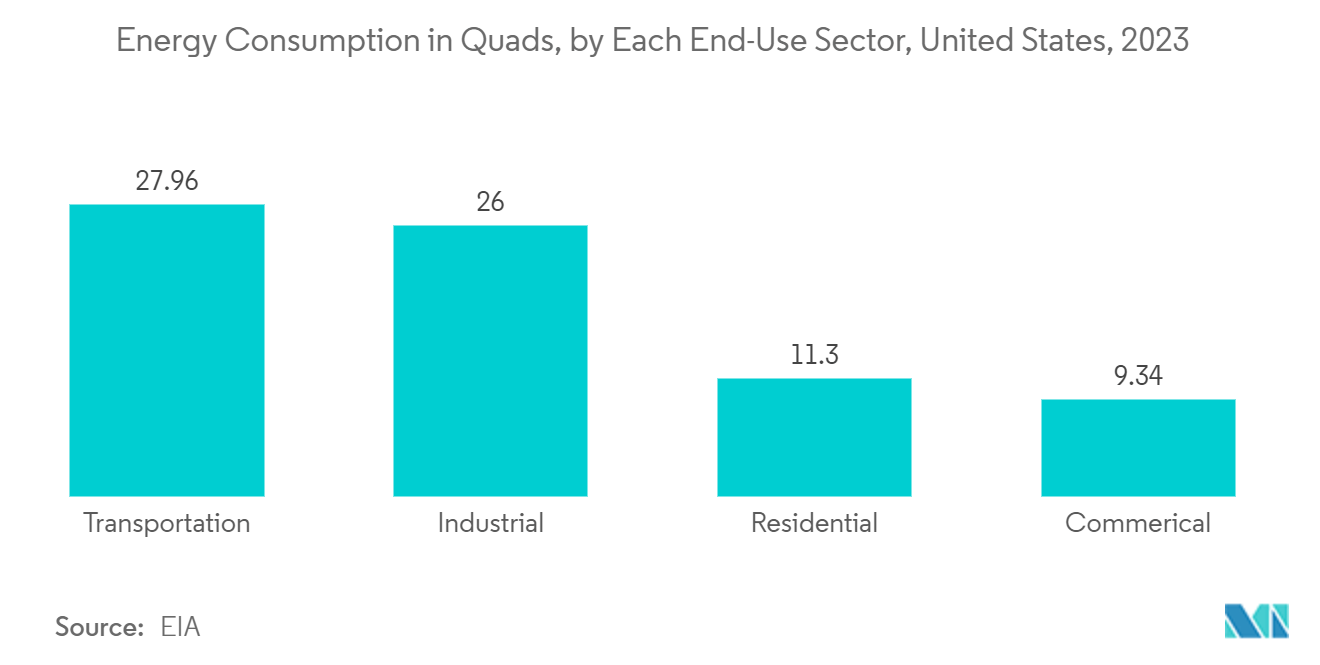
Food, Beverage and Paper Processing (Electrical MRO) Segment to Witness Major Growth
- Proper and continuous functioning of the electrical systems, including control panels, distribution boards, power supplies, circuit breakers, and emergency stop systems, is of utmost importance in the food & beverage industry, which may result in significant product wastage and production downtime.
- The US food processing industry is a global giant. In 2023, retail food and beverage stores in the United States reported annual sales of USD 985.3 million, as per the US Census Bureau. This figure has been on a consistent upward trajectory for decades. Beyond its financial might, the industry is a cornerstone of the US economy, offering employment to millions and driving substantial revenue.
- Maintaining stringent hygiene standards is paramount in electrical systems to avert contamination risks. Components require frequent cleaning, and precise temperature regulation is crucial for food safety. As the industry's machinery grows in size and complexity, electrical systems must adapt, demanding robust and dependable components. Given the propensity of paper processing to generate dust, which can harm electrical equipment, regular cleaning, and maintenance are imperative to prevent failures due to buildup.
- In March 2024, the US government awarded USD 170 million to Kraft Heinz to upgrade ten facilities. Kraft Heinz plans to use the funds to install a range of technologies, including heat pumps, electric heaters, electric boilers, anaerobic digestors, biogas boilers, solar thermal, solar photovoltaic, and thermal energy storage. Similarly, in June 2024, SunOpta disclosed a USD 26 million investment to expand its California plant-based beverage processing facility. These developments, alongside numerous other expansions and upgrades in the sector, are poised to bolster demand and create opportunities in the US electrical service MRO market.
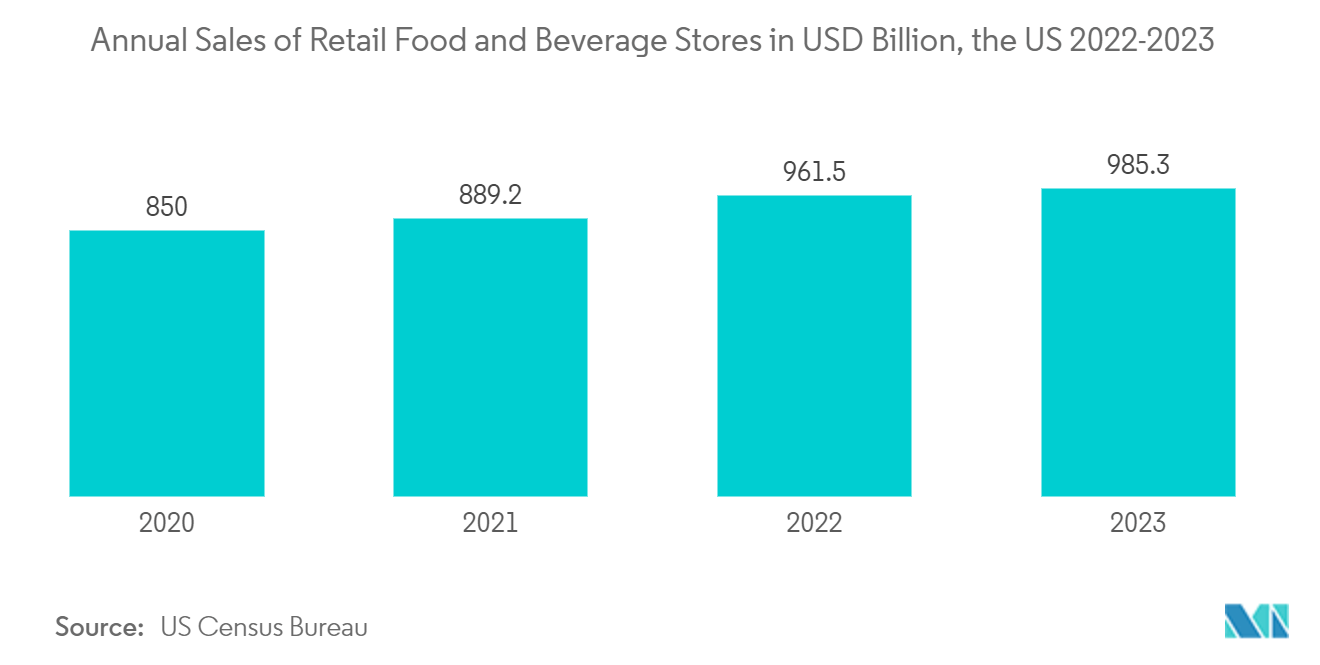