Market Trends of United States Flexographic Printing Industry
This section covers the major market trends shaping the US Flexographic Printing Market according to our research experts:
Packaging Industry to Witness Significant Growth
- Flexography has been widely used as a quick and economical way of applying simple designs and areas of color to a wide variety of packaging materials, such as paper and plastic containers (including waxed-paper ones), corrugated-cardboard boxes, tape, envelopes, and metal foil.
- Flexography, also known as 'flexo,' is a fast-growing process for package printing. It produces good-quality graphics on coated and uncoated paperboard surfaces and flexible films. Tooling costs are slightly higher than offset; however, advancements in inks, presses, digital plates, and sleeves are reducing make-ready times and increasing print quality.
- Packaging printing is taking a crucial role in the future of product safety and promotions through flexible packaging, attributed to on-demand printing in almost any size or quantity. Due to the lower cost of flexo printing, its platforms have increasingly entered the market. When creating personalized, limited-run packaging, they have also become more appealing.
- According to the FTA report, flexible packaging represents approximately 20% of the total USD 184.65 billion United States packaging industry and is the second-largest packaging segment after corrugated paper. Films and resins account for the most significant input spend for converters, with those two categories accounting for over two-thirds of material purchases.
- Rigid packaging is deployed across various industrial domains, including food and beverages, consumer goods, healthcare & pharmaceuticals, and chemicals. Rigid solutions include glass containers, plastic boxes, cans, and cardboard, which are increasingly used for packaging foods, cosmetics, and personal care products.
- Materials go far beyond paper, and many packaging substrates pose a challenge in printing. Flexographic, or flexo printing, solves those challenges and thus has become the de facto standard for packaging companies that want to print on various paper substrates. Compared to other methods, flexographic printing offers more diversity, higher quality, and a lower cost to packaging companies.
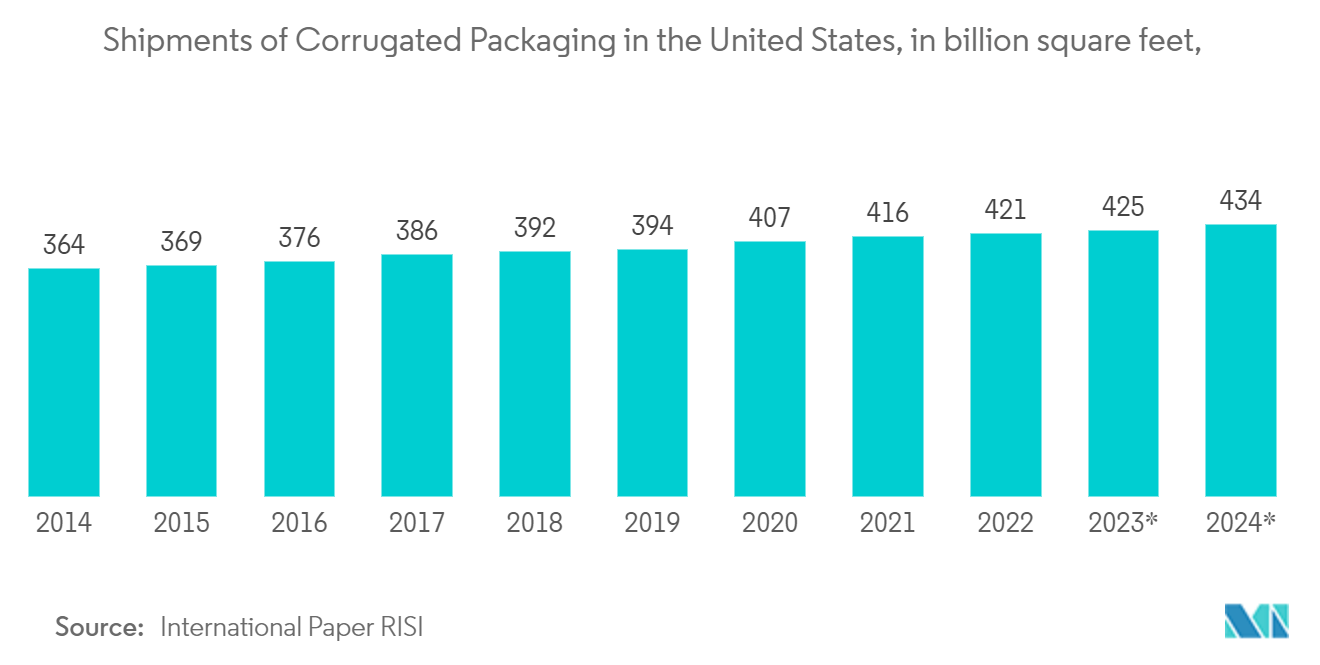
UV-curable Ink Technology Holds Major Market Share
- The country's increased environmental restrictions boost the need for free printing of volatile organic compounds (VOC) ink. UV-cured printing inks are a superior alternative to traditional inks. They are used in various printing processes, such as gravure, inkjet, and flexography, as they offer advantages over conventional inks.
- UV-cured inks do not contain VOCs, and their drying process is quicker as they are treated using UV light, increasing their use in flexographic printing. In addition, as these inks are suitable for flexible as well as rigid packaging applications, their demand is growing in the market.
- These inks get dry by ultraviolet rays and are suitable for packaging decoration printing and shrink sleeve printing on multiple substrates, including coated papers and films with fast curing and a high level of adhesion.
- The players in the market are focusing on introducing products that support circular packaging by developing innovative and eco-friendly inks and coatings. In May 2022, Siegwerk, one of the leading providers of printing inks and coatings for packaging applications and labels, started offering the SICURA Litho Pack ECO series, a new sustainable UV offset ink series for non-food paper and board applications. The new product range is formulated with high bio-renewable content as an environment-friendly alternative to standard UV inks. SICURA Litho Pack ECO is appropriate for all non-food packaging applications where environmental impact and circularity are important considerations.
- UV-cured ink gets cured instantaneously, resulting in a more raised print and appearance with any surface that makes the print less subject to spreading. Such upscaling appearance benefits and instantaneous curing that helps end-users in assisting with the speed of production are the factors primarily responsible for the increasing use of UV-cured inks in flexographic printing.
- Furthermore, hybrid UV inks contain a solvent, such as water or an organic solvent. A significant benefit is the thinner dry layer. Hybrid UV inkjet inks will thus gain market share and are now primarily targeted at packaging applications, particularly for printing on corrugated boards and folding boxes. The revenue from folding paperboard box production in Washington is expected to be approximately USD 155.1 million by 2024.
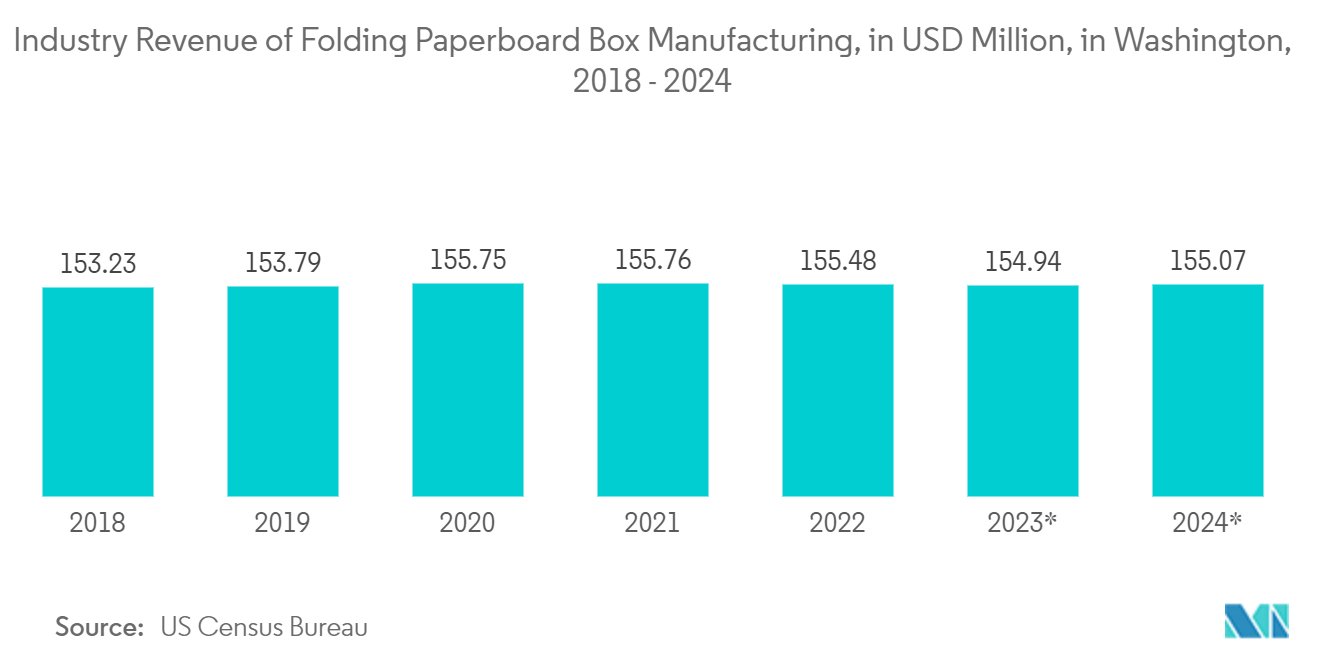