Market Trends of United States Automotive Parts Die Casting Industry
This section covers the major market trends shaping the US Automotive Parts Die Casting Market according to our research experts:
Cost Issues and Resource Inefficiencies
In the light of climatic changes, the global regulatory authorities have set predefined targets for climate protection and energy savings and thereby have made huge initiatives to implement them in recent years. The decisions and measures adopted to protect the climate are having a significant impact on the die casting foundries. The European Union has plans to bring down the primary energy usage to around 20% by the year 2020. The energy savings target (i.e., to cut primary energy usage) has been formulated for the subsequent period, extending to the year 2050.
Die-casting involves sophisticated gating technology, and the level of complexity varies with the pressure of injected molten material. Casting cost varies as per the requirements and changes in material content, net-shape capability and complexity, tooling, and conversion costs. Die-cast tooling is also often regarded as the biggest in terms of cost, and die-cast engineering involves a significant degree of capital that is required for developing suitable gating systems. In addition, the initial costs are also substantially huge for making and manufacturing a suitable non-ferrous die-cast part required by the end-user industries. The gestation period for the investment incurred is also longer due to the implementation of several capital-intensive advanced tools and machinery in the production process.
Although dies have a relatively long wear life and could be economically used in large production facilities, the high start-up cost makes it costlier than conventional vehicle component production. High precision equipment and the extension of casting technologies are increasingly being employed to improve the stability and quality of the component. Thus, the cost involved is significantly high for making and manufacturing suitable die-cast components required for the automotive, industrial, and electronic applications.
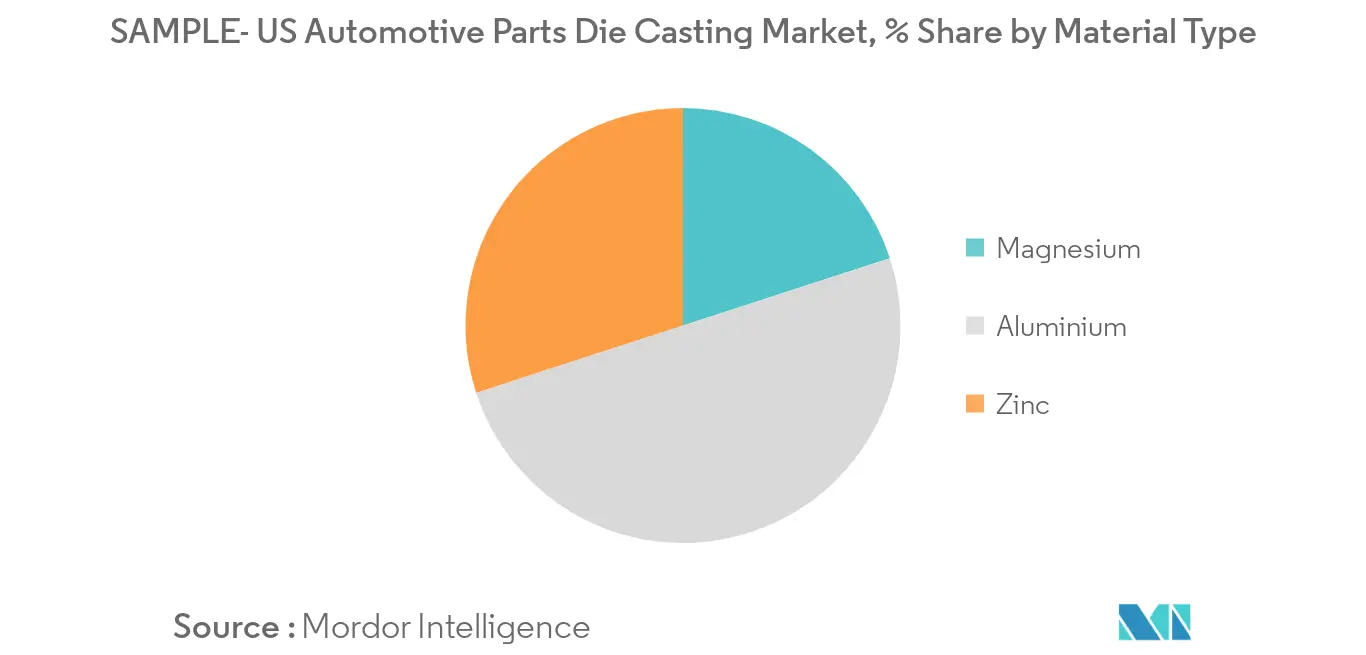
Growing Industry Competition
Empire Die Casting, an Ohio-based aluminum and zinc die caster, and other plants have installed advanced electric aluminum melting, distribution, and holding systems that will cut the amount of energy needed to melt aluminum by 80%. Die casters have successfully implemented a closed-loop system to recycle and reuse as much material as possible within their processes. They recycle everything from office paper to hydraulic fluid to machining chips. This results in very little waste being transported to the landfill. These steps taken by the Die casting firms within the U.S and across North America acted as major driving factors for sustained growth of the market in the country. Increased automation in the die casting industry spiked the productivity and a parallel demand for the former from the automotive industry is dragging the attention of automotive manufacturers towards highly durable aluminum die casting parts.
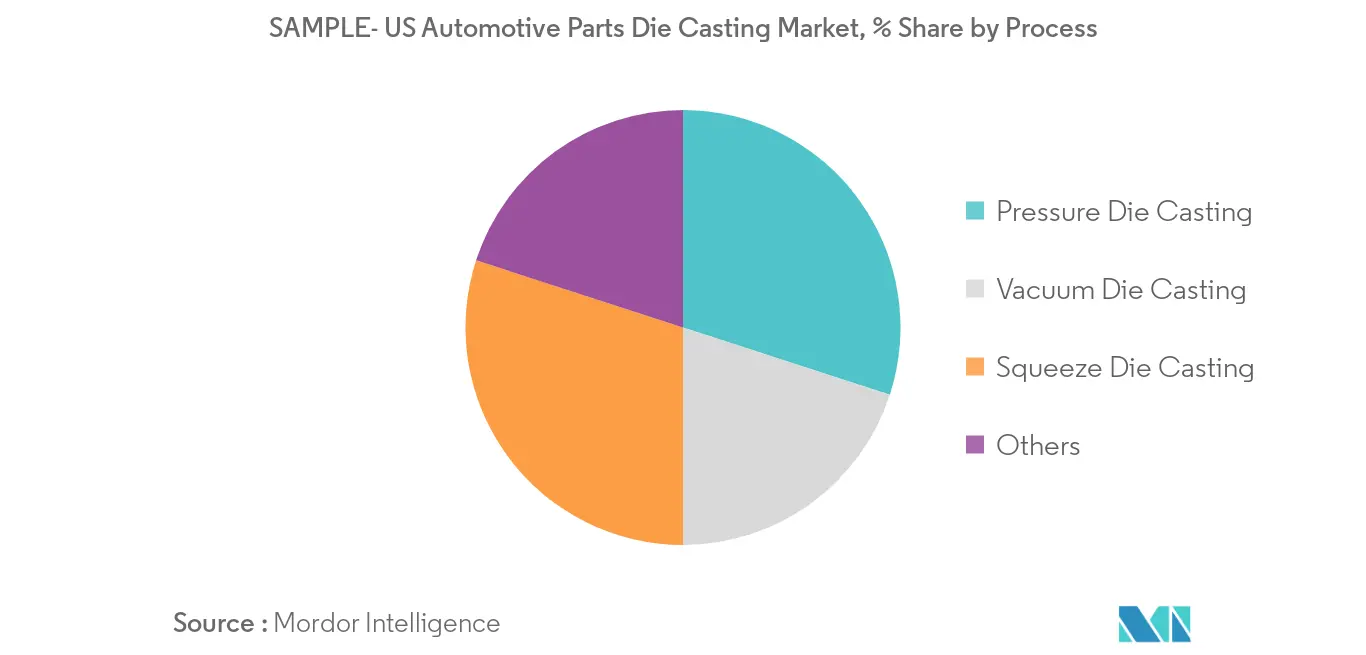