Market Trends of US Automotive Composites Industry
Growing Demand for Lightweight Materials
The automotive industry has been focusing on vehicle weight for decades as vehicle weight have direct impact on driving dynamics and fuel consumption. Due to the high cost of potential lightweight solutions and consumers' limited willingness to pay for weight reduction in automotive, the use of costly lightweight materials has so far been limited. As governments from around the world are implementing stringent emission regulations and even are planning to set even higher emissions standards in the coming years, the importance of lightweight materials will increase. In a typical automobile, the use of fibers is 50% by volume, while adding just 10% to the weight. In the United States, regulations mandate that by 2025, the average fuel economy standard must meet 54.5 miles per gallon. As per the US Department of Energy (DOE), reducing the weight of vehicles by 10% yields an increase of 6-8% in fuel economy. As a result, companies have started using materials like carbon fiber and glass fiber composites to make vehicles lightweight and fuel-efficient. The usage of glass fiber composites aids in reducing vehicle by 25%.
Apart from carbon fiber, automobile manufacturers have been using glass fiber composites in the manufacturing of numerous automotive components. For instance, 2017 Mini Countryman features an interior panel carrier, uses high flow concentrate long glass fiber-reinforced polypropylene (LGFPP) material (STAMAX resin) from SABIC. The part is ~15% lighter in weight than if made from solid plastic. With the demand for lightweight vehicles increasing rapidly in developing economies, the market for carbon fiber composites is projected to grow at a fast pace during the forecast period.
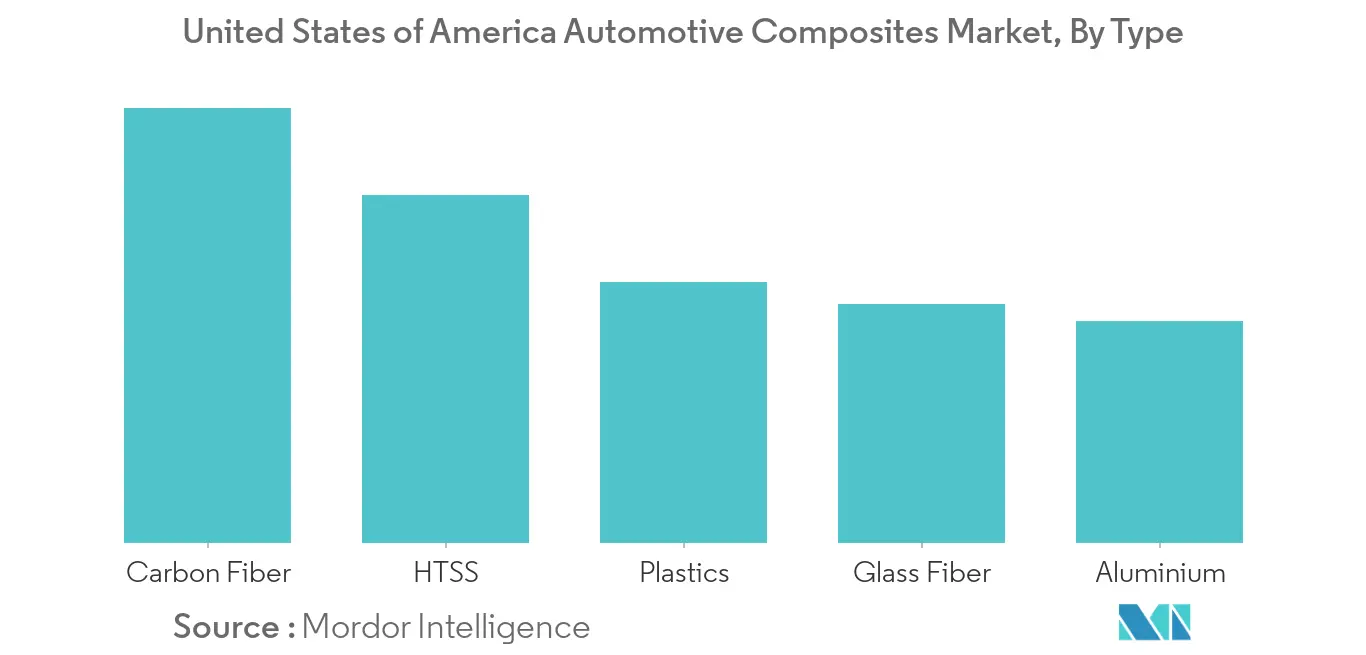
Technological Advancements Will Help Market Grow
Composite parts not only benefit businesses but also help in reducing raw material requirements, energy consumption, and increasing flexibility in prices. It also plays a role in achieving sustainability. Manufacturers are taking advantage of technological advancements. Composites are increasingly being used in interiors, exteriors and under the hood. Air intake, engine oil pan, radiator, engine cover, air cooler end caps and aero ducts. Technological advancements have helped produce composites that are heat and temperature resistant. Polyamide is one of the composites which can withstand a temperature of 250 degree Celsius. Exterior applications include fender, liftgate, door module, hood, and bumper. Other application includes pressure vessels, underbody shield, driveshaft and lead springs.
Glass fibre and Carbon fibre composite materials are very common in the automotive industry. During the forecasted period, the glass fibre composite material is expected to be in high demand. Glass fibre material offers low cost, chemical and corrosion resistance and moderate mechanical performance. The low recyclability of composites is also a restraint for their penetration in entry-level passenger vehicles. However, collaborations of the OEMs with suppliers will open opportunity for the market to grow. Raising consumer confidence, improving quality, durability, and advancement of technology together, these factors are expected to drive the market for automobile composites toward growth.
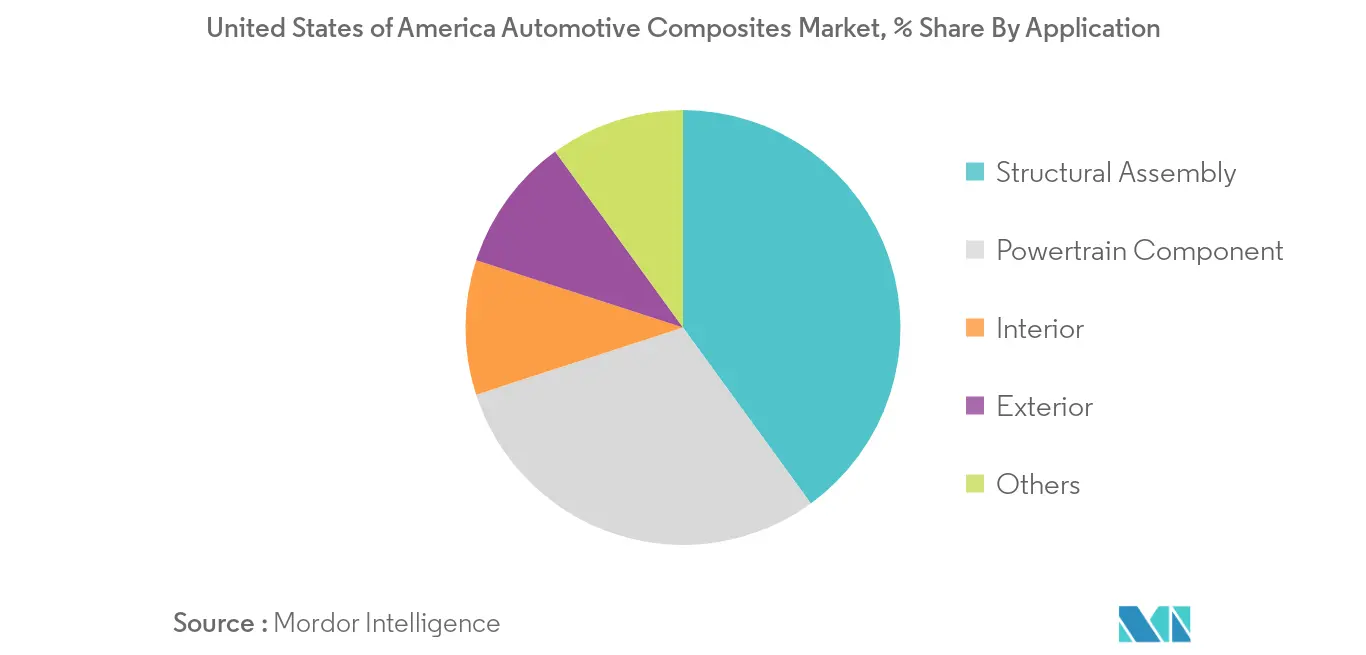