Selective Laser Sintering (SLS) Market Analysis
The Selective Laser Sintering Market size is estimated at USD 4.81 billion in 2025, and is expected to reach USD 13.25 billion by 2030, at a CAGR of 22.46% during the forecast period (2025-2030).
The Selective Laser Sintering (SLS) industry is experiencing transformative growth driven by technological advancements and increasing industrial applications. The technology's evolution has been particularly notable in material science, where the development of advanced 3D printing materials and composites has expanded manufacturing possibilities. This advancement is reflected in China's substantial commitment to research and development, with R&D spending increasing by 10.3% to CNY 2.4 trillion in recent years, demonstrating the growing emphasis on innovative manufacturing technologies. The integration of SLS technology with Industry 4.0 principles has enabled manufacturers to achieve unprecedented levels of precision and customization in their production processes.
The aerospace sector has emerged as a pioneering force in SLS adoption, with companies revolutionizing traditional manufacturing approaches. NASA and private space companies are actively working to reduce rocket engine components through Selective Laser Sintering technology, significantly decreasing production time and costs while improving performance. The technology's capability to consolidate multiple parts into single, unified components has proven particularly valuable in this sector, enabling the production of complex geometries that were previously impossible to manufacture using conventional methods.
The automotive industry has demonstrated remarkable innovation in SLS applications, particularly in prototype development and production parts. BMW Group has showcased the technology's potential by producing up to 150,000 plastic and metal components annually using SLS 3D printing machines, representing a significant shift towards additive manufacturing in mainstream production. This industrial-scale adoption has been accompanied by advancements in material development, including the introduction of new high-performance polymers and composite materials specifically designed for SLS applications.
Strategic industry developments have further accelerated market evolution, as evidenced by Primaeam Solutions' establishment of a 10,000 square foot Additive Manufacturing Customer Experience Centre in Chennai, India. This facility represents a significant investment in comprehensive additive manufacturing capabilities, integrating multiple technologies including SLS, EBM, and MJF under one roof. The industry has also witnessed increased collaboration between technology providers and end-users, leading to more specialized applications and improved process optimization, particularly in high-demand sectors such as aerospace, automotive, and healthcare.
Selective Laser Sintering (SLS) Market Trends
Reduced Time for the End Product to Reach the Market
The selective laser sintering technique has revolutionized manufacturing timelines by significantly shortening the time required for end products to reach the market, resulting in substantial capital savings. A key advantage of selective laser sintering is that the unsintered powder acts as natural support during the printing process, eliminating the need for additional support structures and reducing post-processing time. This is particularly evident in the automotive industry, where companies like BMW have reported remarkable improvements, reducing project time by 92% and achieving cost savings of 58% through SLS implementation. The technology enables fast post-processing with no need to remove supports, no curing requirements, and no soluble baths, allowing parts to be sandblasted directly from the powder bed fusion, which significantly accelerates the production cycle.
The efficiency of SLS in reducing time-to-market is demonstrated through various industrial applications, particularly in the aerospace sector. Bell Textron, an early adopter of additive manufacturing, has successfully produced over 550 parts using SLS technology, with more than 200 of these components being used directly in production. This rapid prototyping and production capability has been further enhanced by recent technological advancements, such as GKN Aerospace's 2022 installation of the RenAM 500 Flex system, featuring four lasers for optimized aerospace applications. The technology's ability to produce multiple parts simultaneously while maintaining high precision and quality has made it particularly valuable for industries requiring quick turnaround times and complex geometries. This is supported by the growing investment in research and development, with Canadian businesses projected to spend $22.4 billion on industrial R&D in 2022, indicating the increasing recognition of SLS's potential to accelerate product development cycles. The use of 3D printing equipment and additive manufacturing systems in these processes highlights the importance of industrial 3D printing in modern manufacturing.
Segment Analysis: By End User Industry
Automotive Segment in Selective Laser Sintering Market
The automotive segment dominates the selective laser sintering market, commanding approximately 34% of the market share in 2024. This significant market position is driven by the extensive use of SLS technology in manufacturing engine parts, prototype intake manifolds, and prototype engine covers. The technology's ability to produce heat-resistant and vibration-tolerant components makes it particularly valuable for automotive applications. Major automotive manufacturers are leveraging SLS for producing complex shapes and intricate details in their prototyping and production processes. The technology's capability to create lightweight components while maintaining structural integrity has become increasingly important as automotive companies focus on fuel efficiency and environmental sustainability. Additionally, the growing trend toward customization in the automotive industry has further cemented SLS's position, with manufacturers using the technology to produce tailored components for specific vehicle models and customer requirements.
Aerospace and Defense Segment in Selective Laser Sintering Market
The aerospace and defense segment is experiencing the highest growth trajectory in the selective laser sintering market, with an expected growth rate of approximately 23% during 2024-2029. This remarkable growth is primarily attributed to the increasing adoption of SLS technology for producing lightweight, durable parts for aircraft and space applications. The sector's stringent requirements for heat-resistant and flame-retardant components have made SLS an ideal choice for manufacturing critical aerospace parts. The technology's ability to produce complex geometries without support structures has revolutionized the production of exterior and interior aircraft components, antennas, satellites, and drone parts. Furthermore, the aerospace industry's shift towards on-demand manufacturing and the need for rapid prototyping capabilities has accelerated the adoption of SLS technology, particularly in developing next-generation aircraft components and space exploration equipment.
Remaining Segments in End User Industry
The healthcare, electronics, and other end-user industries collectively represent significant applications of selective laser sintering technology. The healthcare sector utilizes SLS for producing medical devices, dental restorations, and surgical instruments, benefiting from the technology's ability to create patient-specific devices. The electronics industry leverages SLS for prototyping and functional testing of electronic enclosures and components, particularly valuing its capability to produce precise, lightweight parts. Other industries, including consumer goods and education, are increasingly adopting SLS technology for various applications ranging from product development to specialized manufacturing needs. These segments continue to drive innovation in SLS applications, contributing to the overall market growth through diverse use cases and expanding application possibilities. The use of 3D printing materials like metal powder and polymer powder in these industries further enhances the versatility of additive manufacturing.
Selective Laser Sintering Market Geography Segment Analysis
Selective Laser Sintering Market in North America
North America continues to dominate the global selective laser sintering market, holding approximately 38% of the market share in 2024. The region's leadership position is driven by the presence of numerous companies developing, adopting, and investing in additive manufacturing technologies. The market is characterized by a higher focus on research and development activities and increased testing across various industries, particularly in the automotive and aerospace sectors. The strong presence of advanced manufacturing infrastructure, coupled with substantial investments in industrial automation and Industry 4.0 technologies, has created a favorable environment for market growth. The region's manufacturing sector's emphasis on reducing production costs while maintaining high-quality standards has led to increased adoption of SLS technology. Additionally, the presence of leading market players and their robust distribution networks has facilitated easier access to SLS solutions for end-users.
Selective Laser Sintering Market in Europe
Europe represents a significant market for selective laser sintering technology, demonstrating robust growth with approximately a 22% growth rate from 2019 to 2024. The region's market is primarily driven by strong adoption in high-performance manufacturing sectors, particularly in the automotive and aerospace industries. The European market benefits from advanced research and development infrastructure, supported by strong collaboration between academic institutions and industry players. The region's focus on sustainable manufacturing practices and Industry 4.0 integration has created significant opportunities for SLS technology adoption. The presence of established automotive and aerospace manufacturers, coupled with their increasing focus on lightweight components and complex geometries, has further accelerated market growth. The market is also characterized by strong regional cooperation and knowledge sharing among industry players, contributing to technological advancements and innovation in SLS applications.
Selective Laser Sintering Market in Asia-Pacific
The Asia-Pacific region represents the fastest-growing market for selective laser sintering technology, with a projected growth rate of approximately 24% during 2024-2029. The region's market is characterized by rapid industrialization and increasing adoption of advanced manufacturing technologies across various sectors. The growing emphasis on domestic manufacturing capabilities, particularly in countries like China, Japan, and South Korea, has created substantial opportunities for SLS technology adoption. The region's automotive and electronics manufacturing sectors are increasingly incorporating additive manufacturing technologies into their production processes. The market is further supported by significant investments in research and development infrastructure, particularly in emerging economies. The presence of a large manufacturing base, coupled with an increasing focus on technological advancement and automation, positions the region as a key growth driver for the global SLS market.
Selective Laser Sintering Market in Rest of World
The Rest of World region, encompassing Latin America, the Middle East, and Africa, represents an emerging market for selective laser sintering technology with significant growth potential. These regions are witnessing increasing adoption of advanced manufacturing technologies, driven by growing industrialization and digital transformation initiatives. The market is characterized by rising investments in manufacturing infrastructure and increasing awareness about the benefits of additive manufacturing technologies. The oil and gas industry in the Middle East has emerged as a key adopter of SLS technology for producing specialized components and spare parts. Latin American countries are showing growing interest in SLS technology, particularly in the automotive and aerospace sectors. The market is supported by increasing government initiatives to promote advanced manufacturing technologies and improve domestic production capabilities.
Selective Laser Sintering (SLS) Industry Overview
Top Companies in Selective Laser Sintering Market
The selective laser sintering market features prominent players like 3D Systems Inc., EOS GmbH, Farsoon Technologies, Prodways Group, Formlabs Inc., and Ricoh Company Ltd. These companies are actively pursuing product innovation through advanced technologies, with a particular focus on improving build chamber conditions, mechanical properties, and user interface experiences. The industry witnesses continuous development of new materials and software solutions to enhance 3D manufacturing capabilities and end-product quality. Companies are expanding their geographical footprint through strategic partnerships and distribution networks, particularly in emerging markets. Operational agility is demonstrated through modular system offerings and integrated post-processing solutions, while strategic moves include significant investments in R&D facilities and manufacturing capabilities. Market leaders are increasingly focusing on developing industry-specific solutions, particularly for aerospace, automotive, and healthcare sectors, while simultaneously working to make SLS technology more accessible and cost-effective for smaller enterprises.
Consolidated Market with Strong Global Players
The selective laser sintering market exhibits a relatively consolidated structure dominated by established global players who possess extensive technological expertise and robust distribution networks. These market leaders have built their positions through sustained investments in research and development, coupled with strong intellectual property portfolios that create significant barriers to entry. The market features a mix of diversified technology conglomerates like Ricoh and specialized additive manufacturing companies like EOS GmbH, each bringing unique strengths to the competitive landscape. Regional players are increasingly emerging, particularly in Asia-Pacific, focusing on specific market segments or geographical territories while offering competitive pricing strategies.
The industry has witnessed strategic mergers and acquisitions aimed at expanding technological capabilities and market reach. Companies are actively pursuing vertical integration strategies to control the entire value chain, from material development to post-processing solutions. Partnerships between printer manufacturers and material developers are becoming increasingly common, creating comprehensive ecosystem solutions. The market also sees collaboration between established players and startups, combining innovative technologies with established distribution networks and customer relationships. This dynamic has created a market environment where success depends on both technological innovation and strategic partnerships.
Innovation and Customization Drive Market Success
For incumbent companies to maintain and expand their market share, a multi-faceted approach combining technological leadership with market responsiveness is essential. Success factors include continuous investment in research and development to improve printer capabilities, material properties, and processing speeds. Companies must focus on developing industry-specific solutions while maintaining flexibility to adapt to changing customer requirements. The ability to provide comprehensive solutions, including software integration, material optimization, and technical support, has become increasingly important. Market leaders are also focusing on reducing the total cost of ownership while maintaining quality standards to address the growing demand from small and medium-sized enterprises.
For contenders looking to gain ground, differentiation through specialized applications or unique technological advantages offers the most promising path forward. The market presents opportunities for companies that can address specific industry pain points or develop cost-effective solutions for underserved market segments. End-user concentration in key industries like aerospace and automotive necessitates strong relationships and industry-specific expertise. While substitution risk from other 3D printing technologies exists, SLS's unique capabilities in producing complex, functional parts provide a competitive advantage. Regulatory requirements, particularly in medical and aerospace applications, create both challenges and opportunities for market participants, making compliance capabilities a crucial success factor.
Selective Laser Sintering (SLS) Market Leaders
-
3D Systems Inc.
-
EOS GmbH Electro Optical Systems
-
Farsoon Technologies
-
Prodways Group
-
Formlabs Inc.
- *Disclaimer: Major Players sorted in no particular order
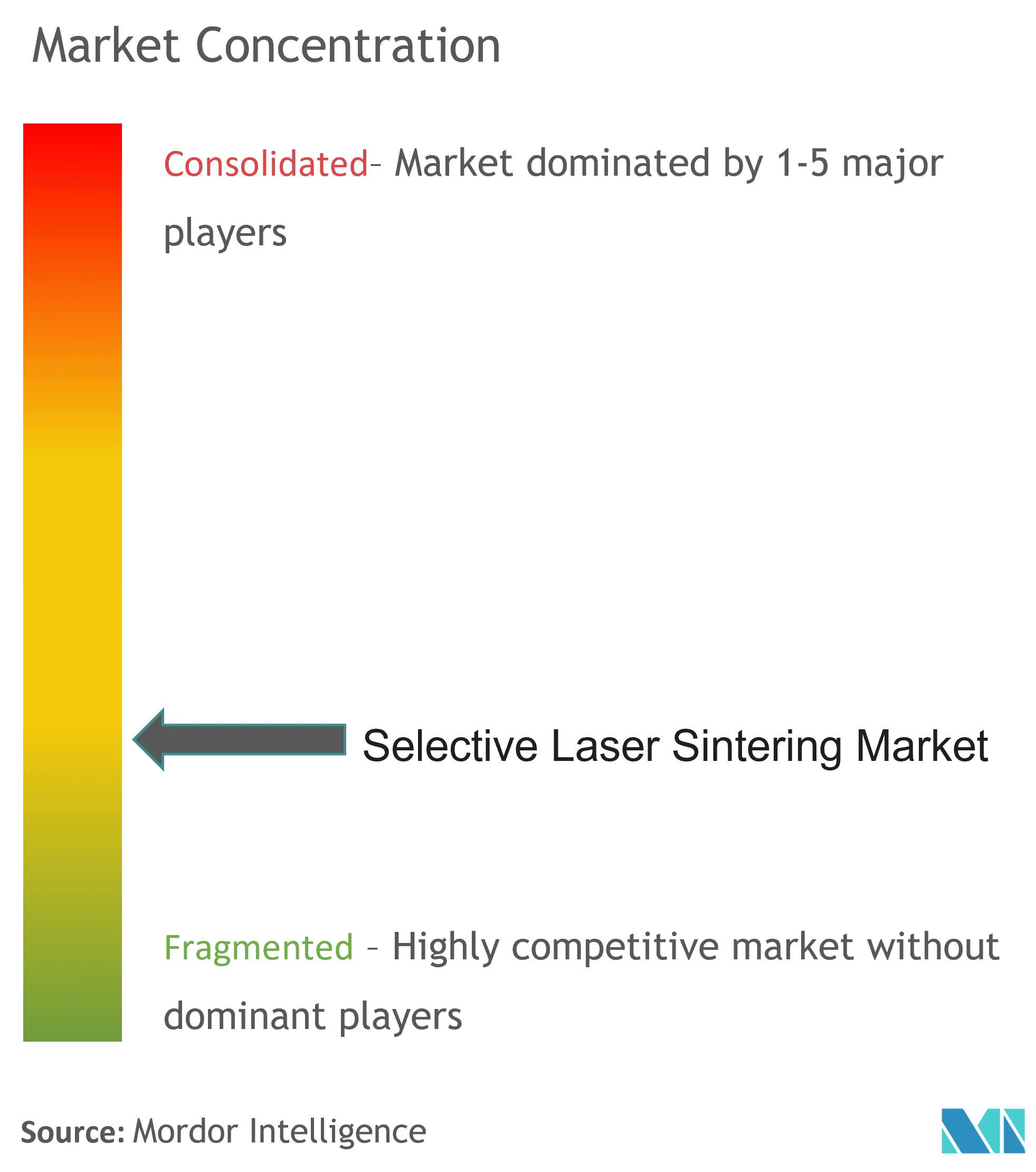
Selective Laser Sintering (SLS) Market News
- August 2022 - Belfast-based Laser Prototypes Europe Ltd (LPE) has expanded its metal 3D printing service with the installation of a second EOS M 290 machine to handle the increased demand for metal sintering parts. Recently LPE has also expanded its in-house selective laser sintering capabilities by installing three post-processing systems from DyeMansion.
- June 2022 - Igus has launched the 3D printing resin specifically for DLP 3D printing of wearing parts. This enables the additive manufacturing of particularly small, precise components with a service life of 30x to 60x longer than conventional 3D printing resins.
Selective Laser Sintering (SLS) Market Report - Table of Contents
1. INTRODUCTION
- 1.1 Study Assumptions and Market Definition
- 1.2 Scope of the Study
2. RESEARCH METHODOLOGY
3. EXECUTIVE SUMMARY
4. MARKET INSIGHTS
- 4.1 Market Overview
-
4.2 Industry Attractiveness - Porters Five Forces Analysis
- 4.2.1 Bargaining Power of Suppliers
- 4.2.2 Bargaining Power of Buyers
- 4.2.3 Threat of New Entrants
- 4.2.4 Threat of Substitutes
- 4.2.5 Intensity of Competitive Rivalry
- 4.3 Assessment of Impact of COVID-19 on the Market
- 4.4 Analysis of 3D Printing Technologies (FDM, SLA, SLS; Qualitative Analysis on Materials and Technologies; Benchtop Industrial SLS Vs Traditional Industrial SLS Printers)
5. MARKET DYNAMICS
-
5.1 Market Drivers
- 5.1.1 Reduced Time for the End Product to Reach the Market
- 5.1.2 Increased Government Initiatives Across Various Regions
-
5.2 Market Challenges
- 5.2.1 Additional Capital Expenditure and Restrictions in Mass Production
6. MARKET SEGMENTATION
-
6.1 By Material
- 6.1.1 Metal
- 6.1.2 Plastic
-
6.2 By Component
- 6.2.1 Hardware
- 6.2.2 Software
- 6.2.3 Services
-
6.3 By End-user Industry
- 6.3.1 Automotive
- 6.3.2 Aerospace and Defense
- 6.3.3 Healthcare
- 6.3.4 Electronics
- 6.3.5 Other End-user Industries
-
6.4 By Geography
- 6.4.1 North America
- 6.4.2 Europe
- 6.4.3 Asia Pacific
- 6.4.4 Rest of the World
7. COMPETITIVE LANDSCAPE
-
7.1 Company Profiles
- 7.1.1 3D Systems Inc.
- 7.1.2 EOS GmbH Electro Optical Systems
- 7.1.3 Farsoon Technologies
- 7.1.4 Prodways Group
- 7.1.5 Formlabs Inc.
- 7.1.6 Ricoh Company Ltd
- 7.1.7 Concept Laser GmbH (General Electric)
- 7.1.8 Renishaw PLC
- 7.1.9 Sinterit Sp. Zoo
- 7.1.10 Sintratec AG
- 7.1.11 Sharebot SRL
- 7.1.12 Red Rock SLS
- *List Not Exhaustive
8. INVESTMENT ANALYSIS
9. FUTURE OF THE MARKET
Selective Laser Sintering (SLS) Industry Segmentation
The selective laser sintering market typically comprises 3D printer suppliers, who use sintering of either plastic or metal powder to create parts and prototypes for various industries.
The report cover industries like automotive, aerospace and defense, and healthcare, that are expected to benefit the most from this technology in the future. The report also presents a comprehensive study on the geographical segmentation of the market and the impact of COVID-19 on the market.
By Material | Metal |
Plastic | |
By Component | Hardware |
Software | |
Services | |
By End-user Industry | Automotive |
Aerospace and Defense | |
Healthcare | |
Electronics | |
Other End-user Industries | |
By Geography | North America |
Europe | |
Asia Pacific | |
Rest of the World |
Selective Laser Sintering (SLS) Market Research FAQs
How big is the Selective Laser Sintering Market?
The Selective Laser Sintering Market size is expected to reach USD 4.81 billion in 2025 and grow at a CAGR of 22.46% to reach USD 13.25 billion by 2030.
What is the current Selective Laser Sintering Market size?
In 2025, the Selective Laser Sintering Market size is expected to reach USD 4.81 billion.
Who are the key players in Selective Laser Sintering Market?
3D Systems Inc., EOS GmbH Electro Optical Systems, Farsoon Technologies, Prodways Group and Formlabs Inc. are the major companies operating in the Selective Laser Sintering Market.
Which is the fastest growing region in Selective Laser Sintering Market?
Asia Pacific is estimated to grow at the highest CAGR over the forecast period (2025-2030).
Which region has the biggest share in Selective Laser Sintering Market?
In 2025, the North America accounts for the largest market share in Selective Laser Sintering Market.
What years does this Selective Laser Sintering Market cover, and what was the market size in 2024?
In 2024, the Selective Laser Sintering Market size was estimated at USD 3.73 billion. The report covers the Selective Laser Sintering Market historical market size for years: 2019, 2020, 2021, 2022, 2023 and 2024. The report also forecasts the Selective Laser Sintering Market size for years: 2025, 2026, 2027, 2028, 2029 and 2030.
Our Best Selling Reports
Selective Laser Sintering Market Research
Mordor Intelligence provides a comprehensive analysis of the selective laser sintering (SLS) industry. We leverage decades of expertise in additive manufacturing research. Our detailed report examines the evolution of powder bed fusion technologies. This includes direct metal laser sintering (DMLS) and laser powder bed fusion (LPBF). We analyze trends in metal powder and polymer powder applications. The report, available as an easy-to-download PDF, offers extensive coverage of industrial 3D printing developments and digital manufacturing innovations.
Stakeholders across the additive manufacturing industry benefit from our in-depth analysis of 3D printing equipment and industrial prototyping applications. The report provides valuable insights into rapid prototyping trends and metal 3D printing industry dynamics. It also explores emerging opportunities in the industrial 3D printing market. Our research encompasses a detailed evaluation of additive manufacturing systems, 3D printing materials, and polymer 3D printing technologies. This provides actionable intelligence for strategic decision-making in the digital manufacturing industry.