Market Trends of Global Manufactured Homes Industry
Modernization of Single-Family Manufactured Homes in North America
In North America, the single-family manufactured housing segment is rapidly evolving, with homes now designed to rival the quality and aesthetics of traditional site-built houses. This modernization is driven by innovations from market leaders and regulatory advancements reshaping perceptions and boosting adoption.
For instance, Clayton Homes, a leading player in the U.S. manufactured housing market, has introduced energy-efficient “net-zero” homes featuring high-end finishes and customizable designs. These homes are equipped with modern features such as solar panels and advanced insulation, making them a competitive alternative to site-built homes. The U.S. Department of Housing and Urban Development (HUD) updated its building codes in September 2024 to support the adoption of such innovations, further solidifying manufactured housing as a viable choice for single-family homebuyers.
Additionally, Skyline Champion Corporation has expanded its portfolio of customizable manufactured homes, targeting middle-income buyers. In April 2024, the company announced the launch of a new line of single-family manufactured homes that emphasize sustainability and design flexibility, aligning with consumer demand for homes that combine affordability with aesthetic appeal.
Despite these advancements, zoning restrictions remain a challenge, particularly in suburban areas. However, certain regions are actively revising their policies to integrate manufactured homes into single-family neighborhoods. For instance, new policies in Texas and Florida in 2024 have enabled the development of modern manufactured housing communities, helping to alleviate housing shortages and improve affordability for first-time buyers.
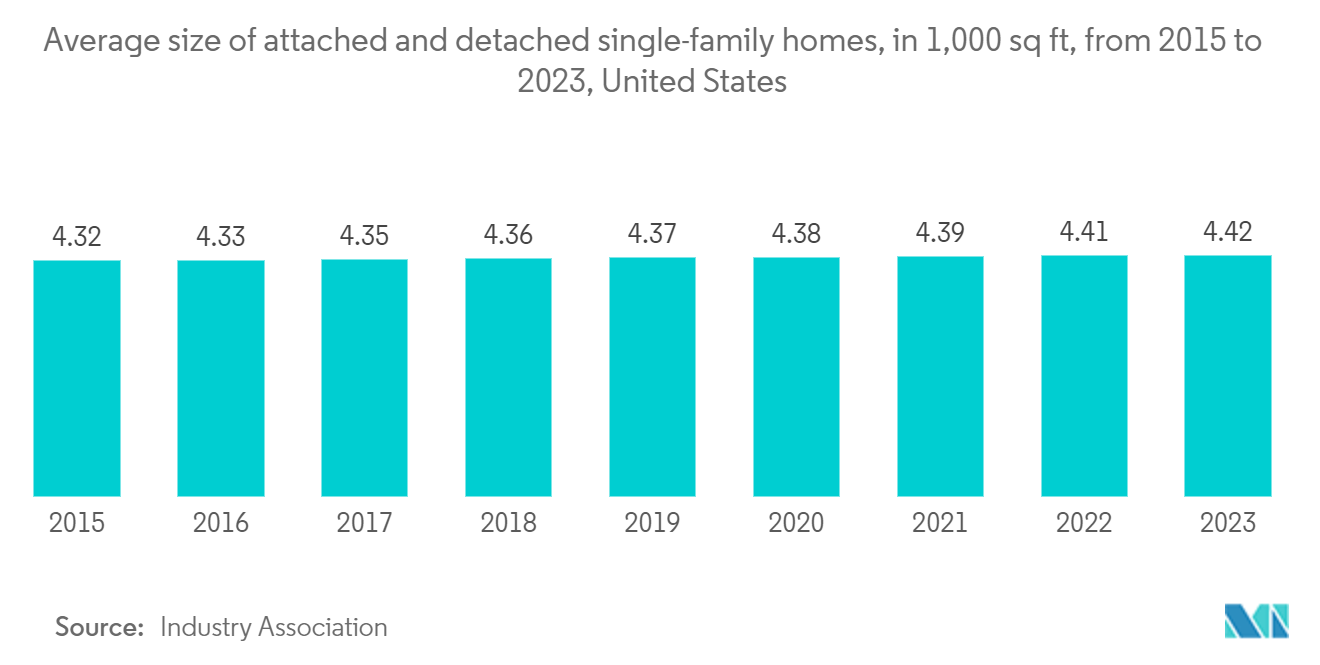
Urbanization Driving the Demand for Affordable Modular Housing in Asia-Pacific
As urbanization surges across the Asia-Pacific, the demand for swift and affordable housing solutions intensifies. Modular housing emerges as a critical solution to these urban challenges. Unlike traditional methods, modular homes, being prefabricated and scalable, ensure faster construction and cost-efficiency.
As of late 2023, Japan relies significantly on modular housing to address its urban housing demands. From 2020 to 2023, prefabricated homes consistently accounted for approximately 15% of the nation's new residential constructions. Urban centers, such as Tokyo and Kanagawa, lead in adopting these homes, supported by innovative manufacturers like Sekisui House and Daiwa House, who are advancing modular designs tailored for urban apartments.
In India, programs like the “Pradhan Mantri Awas Yojana” (PMAY) are driving the adoption of modular housing. In January 2024, Tata Steel’s Nest-In division expanded its prefabricated housing solutions to metropolitan areas like Delhi and Mumbai, effectively addressing urban housing shortages. This expansion highlights the role of modular housing in supporting large-scale urban housing initiatives .
Australia is rapidly emerging as a key market for modular housing, driven by government investments in prefabrication technologies. In April 2024, the Australian Research Council allocated AUD 6 million (USD 3.83 million) to the Advanced Manufacturing of Prefabricated Housing program, achieving a 40% reduction in construction delays and a 50% decrease in carbon emissions. These developments position modular housing as a sustainable and cost-effective solution for urban areas.
With urbanization on the rise, the Asia-Pacific region increasingly views modular housing as a transformative solution, enabling faster, more efficient, and sustainable urban development.
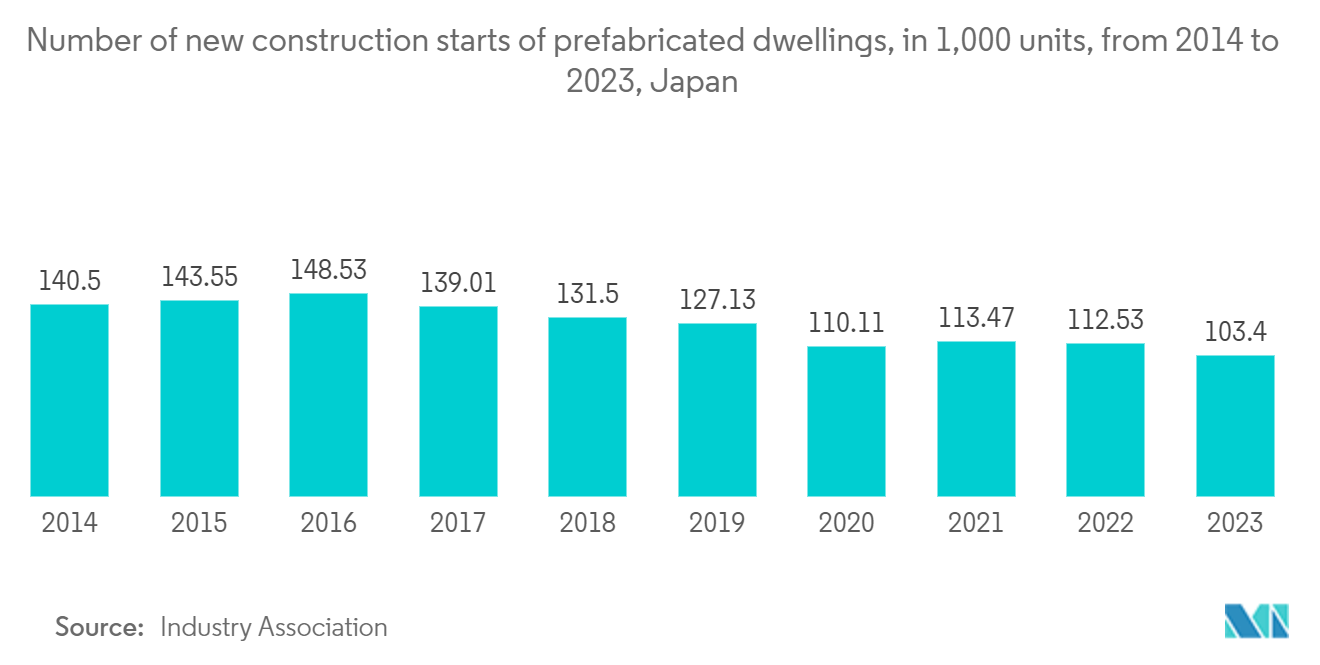