Market Trends of Germany Automotive Parts Die Casting Industry
Increasing Aluminium Use in Die Casting Equipment is Likely to Drive Demand for the Die-Casting Market
- Aluminum is much lighter than steel and has numerous advantages over other materials, such as flexibility. The German automotive sector's largest segment is increasingly focusing on using aluminum rather than steel and iron to produce components and parts using die-casting machinery.
- Owing to the high demand for vehicles in the country, Germany is one of the largest markets for automobiles in the world. The presence of leading automobile manufacturers, as well as component manufacturers, is driving growth in the region. Several premium car manufacturers like Mercedes, Audi, BMW, etc., in the country, are spending heavily on enhancing their product lines. Hence, many die-casting companies are investing in expanding their production capabilities in the country.
- For instance, in September 2022, DGS Druckguss Systeme s.r.o. announced that it had begun operations at the Frdlantplant and produces die castings made of aluminum and magnesium alloy for the automotive industry.
- Major players, such as Rheinmetall AG, GF Automotive, Martinrea, Nemak, DGS Druckguss Systeme HandtmannGroup, and others, have together accounted for a major share of the market in the region. Several key players are expanding their facilities to enhance the product portfolio of the company across the region.
- For instance, in September 2022, Rheinmetall AG (Rheinmetall) received a new EUR 20 million order for its advanced air-divert valve, the Turbo Bypass Valve (TBV) Gen 6, establishing it as an industry heavyweight and the source of several recent orders for Group subsidiary. Production will take place at Pierburg'sNeuss, Germany, plant.
- With an increase in vehicle production across the region, there is a high demand for pressure die-casted parts across the region. The rising cost of fossil fuels, as well as the increasing adoption of electric vehicles, are major market drivers. Furthermore, strict environmental regulations and cafe standards have been imposed in different regions to encourage the use of electric vehicles and lightweight components.
- Furthermore, rising technology and investment in improving and optimizing the metal thermal treatment process are expected to aid in overcoming mold replacement and repair issues, potentially leading to greater use of aluminum in the die-casting process among casting manufacturers during the forecast period.
- Based on such development, the market is expected to boom during the forecast period.
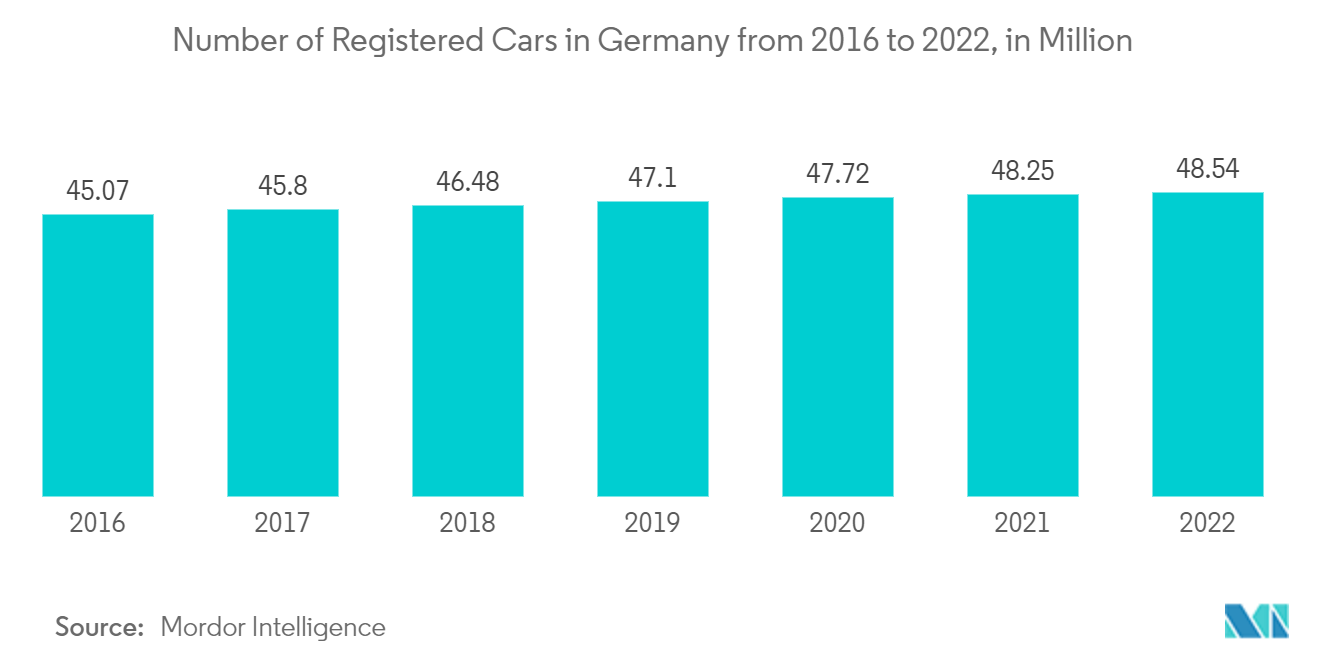
Increasing Adoption of Electric Vehicle May Propel the Market Growth
The automotive industry is the most important market for high-pressure die-casting components. Electric car demand has been fast increasing, owing in large part to improvements in emission standards around the world and a shift in customer preferences. These improvements have compelled automakers to replace heavy components with lightweight, environmentally friendly aluminum alternatives.
The German automotive industry is matured, and thus, is also planning to evolve its products from conventional engines to electric by 2030. Additionally, the demand for and sales of electric vehicles have been continually increasing in the country.
Weight reduction is important for hybrid electric, plug-in hybrid electric, and electric cars since battery efficiency is vital. Aluminum die-cast components can significantly reduce vehicle weight, improving overall vehicle performance, increasing fuel or battery economy, and increasing driving range. Electric Vehicle manufacturers and OEMs are making the investment to develop better products which might boost the demand for automotive parts aluminum die casting in upcoming years.
Major automakers are employing best-in-class machines for fabricating their body parts. For instance, Audi AG relies on additive manufacturing to produce selected tool segments at its metal 3d printing center in Ingolstadt, Germany. Audi utilizes the tool segments, which are produced using an EOS M 400 machine, in its press shop to make body panels for models, including the Audi A4. The company plans to do the same for future electric vehicles.
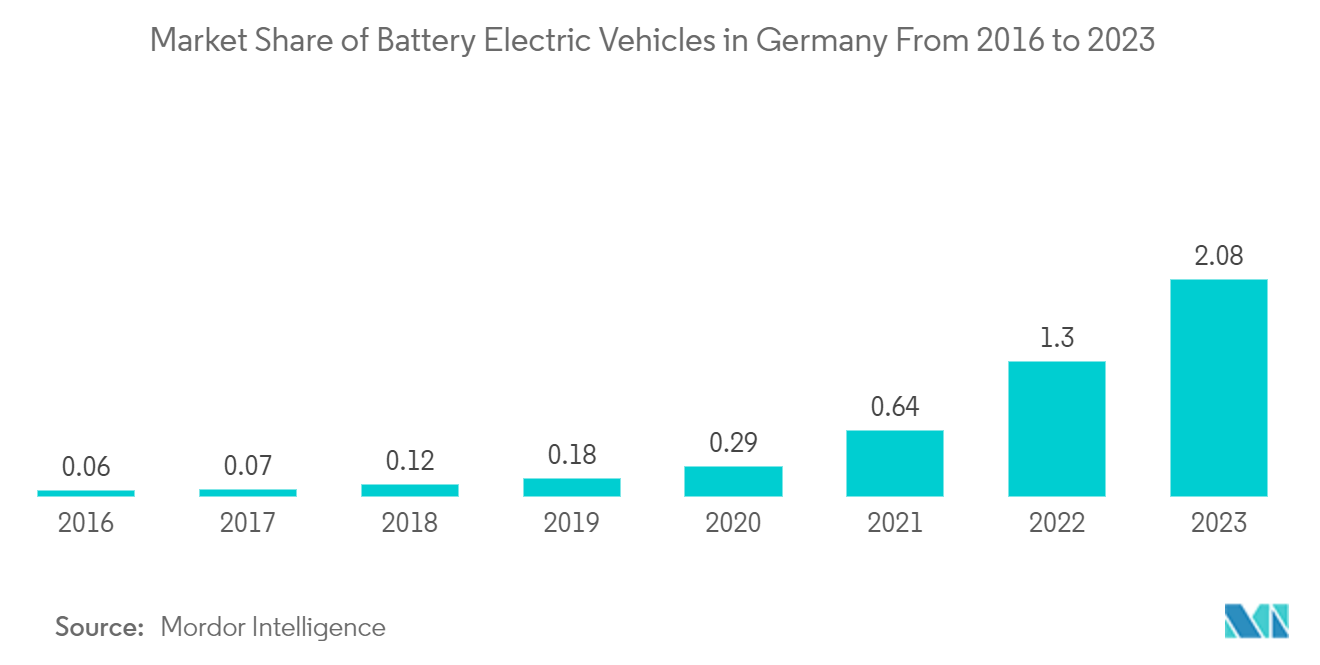