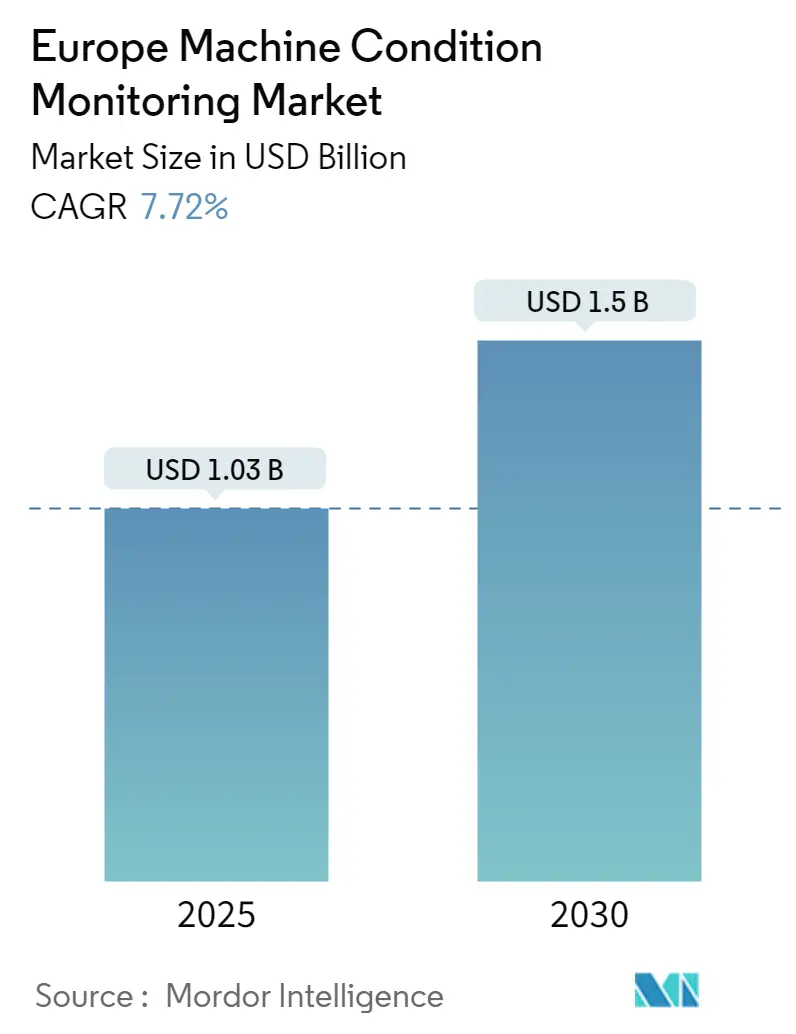
Study Period | 2019 - 2030 |
Base Year For Estimation | 2024 |
Forecast Data Period | 2025 - 2030 |
Market Size (2025) | USD 1.03 Billion |
Market Size (2030) | USD 1.50 Billion |
CAGR (2025 - 2030) | 7.72 % |
Market Concentration | Medium |
Major Players![]() *Disclaimer: Major Players sorted in no particular order |
Europe Machine Condition Monitoring Market Analysis
The Europe Machine Condition Monitoring Market size is estimated at USD 1.03 billion in 2025, and is expected to reach USD 1.50 billion by 2030, at a CAGR of 7.72% during the forecast period (2025-2030).
The European manufacturing landscape is undergoing significant transformation, with machine condition monitoring technologies playing an increasingly vital role in operational efficiency. According to Make UK, the United Kingdom maintains its position as the ninth-largest manufacturing nation globally, with an annual output of GBP 183 billion in 2021, highlighting the robust industrial base requiring advanced monitoring solutions. The integration of sophisticated industrial monitoring systems has become crucial for maintaining a competitive advantage, particularly in high-value manufacturing sectors such as automotive, aerospace, and precision engineering. The adoption of these technologies has been particularly pronounced in countries with strong industrial bases like Germany, France, and Italy, where manufacturing forms a significant portion of the economic output.
The industrial automation sector has witnessed remarkable advancements in industrial sensor technologies and monitoring capabilities. According to the MHI report, the sensors and automatic identification adoption rate is projected to reach 82% by 2025 across the world, with Europe positioned as a major contributor to this growth. This trend is particularly evident in the implementation of smart manufacturing solutions, where real-time monitoring and predictive analytics are becoming standard practices. The network of connected machines is enabling manufacturers to obtain valuable insights into machine performance, enhance ongoing production, and analyze estimated versus actual production ratios with unprecedented accuracy.
The energy sector's transformation has created new opportunities for condition monitoring solutions, particularly in power generation and distribution infrastructure. The European Union's aggressive push toward renewable energy integration has necessitated more sophisticated monitoring systems to maintain the reliability of both traditional and renewable energy assets. The implementation of advanced monitoring solutions has become crucial for maintaining the stability of power generation equipment, particularly in nuclear facilities where France leads with the largest nuclear fleet globally in proportion to its population.
The transportation and aerospace sectors have emerged as significant adopters of equipment monitoring technologies, driven by safety requirements and operational efficiency demands. According to IATA, Europe's air traffic witnessed a substantial increase of 480% from April 2021 to 2022, necessitating robust monitoring systems for aircraft maintenance and safety. In the automotive sector, particularly in Germany, which accounts for around 25% of all passenger cars manufactured in Europe, condition monitoring systems have become integral to maintaining production quality and efficiency. The integration of these technologies has been particularly crucial in supporting the transition to electric vehicle production, where precision manufacturing and quality control requirements are exceptionally high.
Europe Machine Condition Monitoring Market Trends
Increasing Equipment Performance and Productivity Through Predictive Maintenance
Predictive maintenance has emerged as a crucial factor in enhancing equipment performance and productivity across industrial sectors. While reactive maintenance strategies only address machine issues after breakdown, predictive maintenance enables organizations to monitor equipment performance during normal operation to anticipate and prevent failures. Through condition-monitoring tools, organizations can track the performance of equipment in idle, normal, and peak conditions, helping plan maintenance activities effectively to prevent sudden failures or downtime. The implementation of predictive maintenance technologies has shown significant benefits, with studies indicating that the use of predictive maintenance techniques in factories can reduce downtime by up to 50% and generate savings between 10% to 40% on equipment maintenance expenses.
The advancement in predictive maintenance capabilities has been further enhanced through technologies like IoT-based systems that analyze machine operating conditions in real-time to forecast potential malfunctions. These systems employ sensors to collect machine data and utilize sophisticated software to analyze the collected information and generate comprehensive reports. The integration of predictive maintenance has become particularly vital in critical industries like oil and gas, where studies have shown that an average company experiences at least 27 days of unplanned downtime annually, resulting in costs around USD 38 million. Through sophisticated predictive maintenance technologies that leverage AI, machine learning, and advanced analytics, organizations can identify issues early and alert relevant technicians, thereby preventing potential equipment failure and associated safety risks.
Industry 4.0 and Emerging Industrial Applications Across Manufacturing and Process Industries
The evolution of Industry 4.0 is fundamentally transforming manufacturing processes through the integration of emerging technologies such as IoT, cloud computing, analytics, AI, and machine learning into production facilities and operations. This digital transformation is facilitating the transition from legacy systems to smart components and machines, enabling the creation of digital factories and an interconnected ecosystem of manufacturing enterprises. These smart factories are equipped with advanced sensors, embedded software, and robotics that collect and analyze data in real-time, enabling better decision-making processes. According to ETNO, the active Internet of Things (IoT) connections are projected to reach 223 million in the automotive sector and 19 million across industries in Europe by 2027, highlighting the growing industrial adoption of connected technologies.
The implementation of automated industrial IoT monitoring serves as the cornerstone for achieving smart factory capabilities, where machines are interconnected through IoT-enabled, web-based sensors that enable real-time data extraction. This network of connected machines provides valuable insights into performance metrics, enhances ongoing production processes, and enables analysis of estimated versus actual production ratios. The integration of machine performance monitoring has also significantly improved shop floor communications, with manufacturers and operators receiving real-time analytics, warnings, and notifications that expand production process visibility. This enhanced visibility creates better awareness and engagement among stakeholders, allowing them to connect individual shop floor operations with broader performance outcomes. The effectiveness of these smart manufacturing systems is evidenced in major industrial nations like Germany, where the automotive sector, which accounts for approximately 25% of all passenger cars manufactured in Europe, has significantly benefited from implementing advanced condition monitoring solutions to ensure safe and efficient vehicle production operations.
Segment Analysis: By Type
Hardware Segment in Europe Machine Condition Monitoring Market
The hardware segment continues to dominate the Europe machine condition monitoring market, holding approximately 53% market share in 2024. This segment encompasses critical monitoring equipment, including vibration monitoring systems, thermography equipment, and lubricating oil analysis tools. The widespread adoption of hardware solutions is driven by their essential role in providing real-time equipment health monitoring capabilities for industrial machinery and equipment. Vibration monitoring equipment represents the largest hardware subsegment, finding extensive applications in industrial processes involving turbines, motors, and pumps. The hardware segment's prominence is further strengthened by continuous technological advancements in sensor technology, improved accuracy in measurement capabilities, and the increasing integration of IoT-enabled features in monitoring devices.
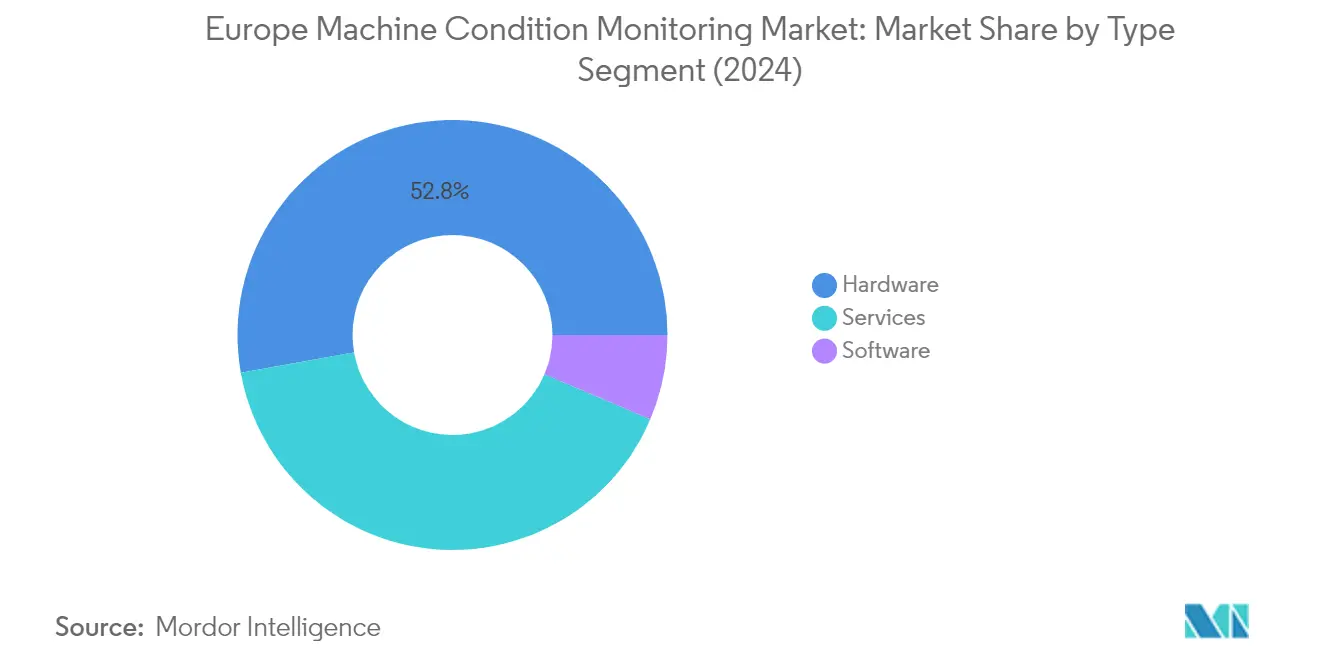
Services Segment in Europe Machine Condition Monitoring Market
The services segment is emerging as the fastest-growing segment in the Europe machine condition monitoring market, projected to grow at approximately 8% from 2024 to 2029. This growth is primarily driven by the increasing demand for remote monitoring services, particularly for equipment located in hard-to-reach or distant locations. The segment's expansion is further supported by the rising adoption of cloud-based monitoring solutions and the growing preference for maintenance-as-a-service models. Service providers are increasingly incorporating advanced analytics and artificial intelligence capabilities into their offerings, enabling more accurate predictive maintenance recommendations and real-time monitoring capabilities. The shift towards digital transformation and Industry 4.0 initiatives across European industries has also contributed to the increased demand for specialized condition monitoring services.
Remaining Segments in Europe Machine Condition Monitoring Market
The software segment, while smaller in market share, plays a crucial role in the overall machine condition monitoring ecosystem. This segment focuses on providing sophisticated analytics platforms, data management solutions, and predictive maintenance software that complement hardware installations. Modern condition monitoring systems increasingly rely on advanced software solutions to integrate various types of monitoring data into unified systems, enabling real-time analysis and decision-making capabilities. The software segment's importance is growing with the increasing emphasis on data-driven maintenance strategies and the need for comprehensive asset performance monitoring solutions in industrial applications.
Segment Analysis: By End-User Vertical
Power Generation Segment in Europe Machine Condition Monitoring Market
The power generation segment has emerged as the dominant force in the Europe machine condition monitoring market, commanding approximately 26% market share in 2024. This prominence is driven by the critical role of equipment health monitoring in maintaining a reliable power supply across the region's diverse energy infrastructure, including nuclear, thermal, and renewable power plants. The segment's leadership position is reinforced by Europe's ongoing energy transition initiatives and the increasing focus on operational efficiency in power generation facilities. Continuous monitoring of power generation equipment has become essential for maintaining a reliable flow of power to consumers while simultaneously alerting operators about potential equipment damage requiring timely repairs. The integration of advanced monitoring systems in both primary machinery and Balance of Plant (BoP) equipment has become standard practice, with many facilities moving from periodic to continuous monitoring using vibration transmitters, signal conditioners, and scanning monitors.
Process and Manufacturing Segment in Europe Machine Condition Monitoring Market
The process and manufacturing segment is witnessing substantial growth in the Europe machine condition monitoring market, driven by the increasing adoption of Industry 4.0 technologies and smart manufacturing practices. The segment's growth is characterized by the rising implementation of intelligent condition monitoring systems, which are vital for improving productivity and availability of production systems. Manufacturing facilities across Europe are increasingly embracing IoT technology to monitor machine health and connect critical equipment for analyzing various parameters, including vibration, noise, and fuel utilization. The integration of Artificial Intelligence (AI) in manufacturing processes has revolutionized intelligent condition monitoring, enabling more sophisticated analysis and decision-making capabilities without interrupting normal machine operations. This transformation is particularly evident in unmanned manufacturing systems, where AI assists in extracting valuable insights and making appropriate decisions from measured signals.
Remaining Segments in End-User Vertical
The other significant segments in the Europe machine condition monitoring market include oil and gas, aerospace and defense, automotive and transportation, and various other end-user verticals such as marine, mining, and metal industries. The oil and gas sector maintains a strong presence due to its extensive use of machinery diagnostics for upstream, midstream, and downstream operations. The aerospace and defense segment is driven by the increasing need for aircraft safety and operational efficiency. The automotive and transportation sector is experiencing transformation through the rise of electric vehicles and autonomous driving technologies, creating new demands for condition monitoring solutions. The marine, mining, and metal industries contribute to market growth through their specific requirements for equipment monitoring in harsh operating environments and critical industrial processes.
Europe Machine Condition Monitoring Market Geography Segment Analysis
Europe Machine Condition Monitoring Market in Germany
Germany, as the powerhouse of European industrial automation, leads the region's machine condition monitoring market with approximately 24% market share in 2024. The country's dominance is driven by its robust automotive sector, which accounts for around 25% of all passenger cars manufactured in Europe. The presence of major automotive and industrial suppliers, such as Schaeffler and ZF, has fostered innovative developments in industrial condition monitoring technologies, particularly in areas like axlebox bearing monitoring. Germany's maritime industry, with its 30% international market share in container shipping, has also significantly contributed to the demand for equipment condition monitoring solutions. The country's strong focus on Industry 4.0 initiatives and manufacturing excellence has led to increased adoption of advanced monitoring systems across various industrial sectors. Furthermore, German manufacturers' emphasis on predictive maintenance and equipment reliability has created a sophisticated ecosystem of condition monitoring solution providers and users.
Europe Machine Condition Monitoring Market in United Kingdom
The United Kingdom demonstrates remarkable growth potential in the machine condition monitoring market, with a projected CAGR of approximately 8% from 2024 to 2029. The country's manufacturing sector maintains its position as the ninth-largest globally, with significant investments in Industry 4.0 technologies and smart manufacturing initiatives. The adoption of 3D printing, the Internet of Things (IoT), and artificial intelligence has accelerated, driven by the nation's commitment to achieving net-zero emissions by 2050. British companies are increasingly implementing sophisticated condition monitoring solutions, particularly in the aerospace and defense sectors, where the UK holds its position as the world's second-largest aerospace industry. The emergence of innovative startups and collaboration between established players has created a dynamic market environment. Local companies like Sensoteq have introduced advanced wireless vibration sensors, demonstrating the country's technological capabilities in this domain. The integration of condition monitoring with smart factory initiatives has further accelerated market growth, particularly in predictive maintenance applications.
Europe Machine Condition Monitoring Market in France
France's machine condition monitoring market is significantly driven by its dominant nuclear power generation sector, hosting one of the world's most important nuclear parks with 56 reactors across 19 sites. The country's emphasis on energy security and operational excellence in nuclear facilities has created substantial demand for sophisticated monitoring solutions. The aerospace industry, a crucial sector of the French economy, has been actively adopting condition monitoring systems to ensure seamless manufacturing operations and maintenance of critical equipment. French companies have been at the forefront of developing innovative IoT-based predictive maintenance solutions, as exemplified by the collaboration between Actility, NKE Watteco, and WMW. The country's industrial sector has shown increasing interest in implementing condition monitoring systems, particularly in applications requiring high precision and reliability. The strong presence of research institutions and technology companies has fostered continuous innovation in monitoring technologies and solutions.
Europe Machine Condition Monitoring Market in Italy
Italy's industrial asset monitoring market is characterized by its strong manufacturing base, particularly in machinery, fashion items, food products, automotive parts, and pharmaceuticals. As the second-largest manufacturing country in Europe, Italy has demonstrated significant progress in Industry 4.0 adoption, with approximately 75% of Italian manufacturers undertaking advanced manufacturing projects. The country's oil and gas sector, recording the highest oil and petroleum production in the European Union, has been a major driver for condition monitoring solutions. Italian companies have shown increasing interest in predictive maintenance technologies, particularly in the steel industry, where the country maintains a significant presence in Europe. The development of innovative solutions by local companies, such as Cannon Afros's OptiWise predictive maintenance system, demonstrates the market's technological advancement. The integration of IoT and Industry 4.0 principles has further accelerated the adoption of condition monitoring systems across various industrial sectors.
Europe Machine Condition Monitoring Market in Other Countries
The asset health monitoring market in other European countries, including Eastern European nations like Poland, Belarus, and Romania, along with Western European countries such as the Netherlands and Switzerland, demonstrates diverse adoption patterns and growth opportunities. Each country brings unique industrial strengths: Poland's significant mining industry, Belarus's manufacturing sector, Romania's automotive industry, the Netherlands' energy sector, and Switzerland's precision engineering capabilities. These countries are increasingly embracing condition monitoring solutions as part of their industrial modernization efforts. The adoption is particularly strong in sectors such as power generation, manufacturing, and process industries. The growing emphasis on predictive maintenance and Industry 4.0 initiatives across these nations continues to drive market expansion. The presence of both international and local solution providers has created a competitive environment that fosters innovation and technological advancement in condition monitoring solutions.
Europe Machine Condition Monitoring Industry Overview
Top Companies in Europe Machine Condition Monitoring Market
The market features prominent players like Honeywell International, Schaeffler Technologies, General Electric, Emerson Electric, Fluke Corporation, AMETEK Spectro Scientific, Parker Hannifin, Rockwell Automation, SKF AB, and FLIR Systems. These companies are heavily investing in research and development to develop innovative machine condition monitoring solutions incorporating IoT, AI, and machine learning capabilities. Strategic partnerships, particularly with cloud service providers and industrial automation firms, have become increasingly common to enhance product offerings and expand market reach. Companies are focusing on developing more user-friendly interfaces, remote equipment monitoring capabilities, and predictive maintenance features in their solutions. The industry has also witnessed significant investment in expanding manufacturing facilities and service centers across Europe to better serve local markets and reduce delivery times.
Consolidated Market with Strong Global Players
The European machine condition monitoring market is characterized by the strong presence of large multinational industrial conglomerates that leverage their extensive distribution networks and technological expertise. These established players have built comprehensive product portfolios through years of organic growth and strategic acquisitions, making it challenging for new entrants to gain significant market share. The market demonstrates a moderate level of consolidation, with the top companies controlling a substantial portion of the market share through their established brand reputation and long-standing customer relationships.
The competitive landscape is further shaped by ongoing merger and acquisition activities, as larger companies seek to acquire specialized technology providers and expand their capabilities in emerging areas like IoT-enabled monitoring systems and advanced analytics. Regional players maintain their presence through specialized offerings and strong local customer relationships, though they face increasing pressure from global competitors expanding their European operations. The market also sees collaboration between traditional equipment manufacturers and technology companies to develop integrated monitoring solutions.
Innovation and Customer Focus Drive Success
Success in the machine condition monitoring market increasingly depends on companies' ability to provide comprehensive, integrated solutions that combine hardware expertise with advanced software capabilities. Market leaders are strengthening their positions by developing industry-specific solutions, particularly for high-value sectors like oil and gas, power generation, and manufacturing. Companies are also focusing on building recurring revenue streams through subscription-based monitoring services and machine prognostics solutions, while expanding their service networks to provide better local support and faster response times.
For new entrants and smaller players, success lies in identifying and serving niche market segments with specialized solutions that address specific industry challenges. The increasing adoption of Industry 4.0 principles and the growing emphasis on industrial diagnostics create opportunities for innovative solutions providers. However, companies must navigate challenges including high customer switching costs, the need for extensive industry certifications, and the growing importance of cybersecurity in connected monitoring systems. The market's future will be shaped by the ability to provide scalable, secure, and cost-effective solutions that deliver clear operational benefits to end-users.
Europe Machine Condition Monitoring Market Leaders
-
Honeywell International Inc.
-
Schaeffler Technologies AG & Co. KG
-
General Electric Company
-
Emerson Electric Co.
-
Fluke Corporation
- *Disclaimer: Major Players sorted in no particular order
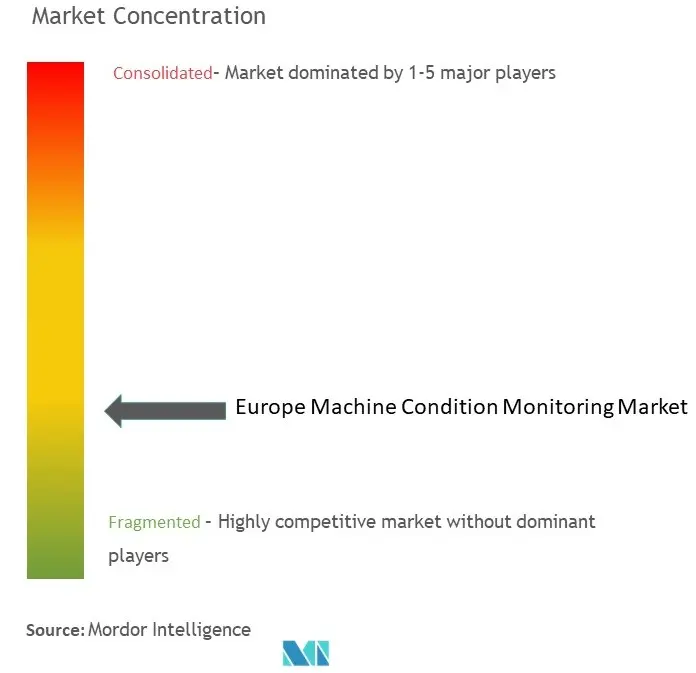
Europe Machine Condition Monitoring Market News
- May 2022: Rockwell Automation Inc. announced the release of its new Allen-Bradley Armor PowerFlexAC variable frequency drives for industrial motor control applications. The drives also monitor component life, allowing users to predict and schedule component replacements to help avoid costly unplanned downtime.
- February 2022: GE Aviation announced its partnership with Boeing for a hybrid electric flight test demonstration program, where Boeing and its subsidiary Aurora Flight Sciences provide GE Aviation with airplane modification, system integration, and flight-testing services, including nacelle manufacturing, flight deck interface design and software, aircraft-level performance analysis, and systems integration.
Europe Machine Condition Monitoring Market Report - Table of Contents
1. INTRODUCTION
- 1.1 Study Assumptions and Market Definition
- 1.2 Scope of the Study
2. RESEARCH METHODOLOGY
3. EXECUTIVE SUMMARY
4. MARKET INSIGHTS
- 4.1 Market Overview
-
4.2 Industry Attractiveness - Porter's Five Forces Analysis
- 4.2.1 Bargaining Power of Suppliers
- 4.2.2 Bargaining Power of Buyers
- 4.2.3 Threat of New Entrants
- 4.2.4 Threat of Substitutes
- 4.2.5 Intensity of Competitive Rivalry
- 4.3 Assessment of the Impact of COVID-19 on the Market
5. MARKET DYNAMICS
-
5.1 Market Drivers
- 5.1.1 Increasing Equipment Performance and Productivity through Predictive Maintenance
- 5.1.2 Industry 4.0 and Emerging Industrial Applications Across Manufacturing and Process Industries
-
5.2 Market Challenges/Restraints
- 5.2.1 Cost Implications In Line With Retrofits
- 5.2.2 European Macroeconomic and Geopolitical Factors
6. MARKET SEGMENTATION
-
6.1 By Type
- 6.1.1 Hardware
- 6.1.1.1 Vibration Condition Monitoring Equipment
- 6.1.1.2 Thermography Equipment
- 6.1.1.3 Lubricating Oil Analysis
- 6.1.2 Software
- 6.1.3 Services
-
6.2 By End-user Vertical
- 6.2.1 Oil and Gas
- 6.2.2 Power Generation
- 6.2.3 Process and Manufacturing
- 6.2.4 Aerospace and Defense
- 6.2.5 Automotive and Transportation
- 6.2.6 Other End-user Verticals (marine, Mining, Metal, Etc.)
-
6.3 By Country
- 6.3.1 United Kingdom
- 6.3.2 Germany
- 6.3.3 France
- 6.3.4 Italy
- 6.3.5 Rest of Europe (Eastern Europe and Western European Countries)
7. COMPETITIVE LANDSCAPE
-
7.1 Company Profiles
- 7.1.1 Honeywell International Inc.
- 7.1.2 Schaeffler Technologies AG & Co. KG
- 7.1.3 General Electric Company
- 7.1.4 Emerson Electric Co.
- 7.1.5 Fluke Corporation
- 7.1.6 Ametek Spectro Scientific
- 7.1.7 Parker Hannifin Corporation
- 7.1.8 Rockwell Automation Inc.
- 7.1.9 SKF AB
- 7.1.10 Als Limited
- 7.1.11 National Instruments Corporation
- 7.1.12 Flirn Systems Inc.
- *List Not Exhaustive
8. INVESTMENT ANALYSIS
9. FUTURE OF THE MARKET
Europe Machine Condition Monitoring Industry Segmentation
Machine condition monitoring is the process of monitoring the condition of a machine with the intent of predicting mechanical wear and failure.
The market is segmented by type (hardware (vibration condition monitoring equipment, thermography equipment, lubricating oil analysis), software, services), end-user vertical (oil and gas, power generation, process and manufacturing, aerospace and defense, automotive and transportation, other end-user verticals), and country (United Kingdom, Germany, France, Italy, Rest of Europe). The market sizes and forecasts are provided in terms of value in USD million for all the above segments.
By Type | Hardware | Vibration Condition Monitoring Equipment |
Thermography Equipment | ||
Lubricating Oil Analysis | ||
Software | ||
Services | ||
By End-user Vertical | Oil and Gas | |
Power Generation | ||
Process and Manufacturing | ||
Aerospace and Defense | ||
Automotive and Transportation | ||
Other End-user Verticals (marine, Mining, Metal, Etc.) | ||
By Country | United Kingdom | |
Germany | ||
France | ||
Italy | ||
Rest of Europe (Eastern Europe and Western European Countries) |
Europe Machine Condition Monitoring Market Research FAQs
How big is the Europe Machine Condition Monitoring Market?
The Europe Machine Condition Monitoring Market size is expected to reach USD 1.03 billion in 2025 and grow at a CAGR of 7.72% to reach USD 1.50 billion by 2030.
What is the current Europe Machine Condition Monitoring Market size?
In 2025, the Europe Machine Condition Monitoring Market size is expected to reach USD 1.03 billion.
Who are the key players in Europe Machine Condition Monitoring Market?
Honeywell International Inc., Schaeffler Technologies AG & Co. KG, General Electric Company, Emerson Electric Co. and Fluke Corporation are the major companies operating in the Europe Machine Condition Monitoring Market.
What years does this Europe Machine Condition Monitoring Market cover, and what was the market size in 2024?
In 2024, the Europe Machine Condition Monitoring Market size was estimated at USD 0.95 billion. The report covers the Europe Machine Condition Monitoring Market historical market size for years: 2019, 2020, 2021, 2022, 2023 and 2024. The report also forecasts the Europe Machine Condition Monitoring Market size for years: 2025, 2026, 2027, 2028, 2029 and 2030.
Our Best Selling Reports
Europe Machine Condition Monitoring Market Research
Mordor Intelligence provides comprehensive insights into the machine condition monitoring industry through expert analysis and consulting services. Our research thoroughly examines industrial monitoring systems. This includes an in-depth look at vibration monitoring technologies and the deployment of industrial sensors across Europe. The report offers a detailed analysis of predictive maintenance strategies alongside equipment diagnostics, supported by advanced predictive analytics methodologies. Our expertise in industrial maintenance and machinery diagnostics ensures stakeholders receive accurate and actionable intelligence about the evolving landscape of industrial condition monitoring.
The report, available as an easy-to-download PDF, offers valuable insights into equipment condition monitoring and machine health monitoring systems. Stakeholders benefit from detailed analysis of asset health monitoring trends and industrial IoT monitoring implementations. The research covers crucial aspects of equipment health monitoring and machine performance monitoring. It also explores emerging machine prognostics technologies. Our analysis of industrial asset monitoring and asset performance monitoring provides stakeholders with strategic insights for optimizing their industrial diagnostic capabilities and monitoring systems. The comprehensive coverage includes equipment monitoring solutions that drive operational excellence across various industrial sectors.