Market Trends of Automated 3D Printing Industry
This section covers the major market trends shaping the Automated 3D Printing Market according to our research experts:
The Automotive Segment is Expected to Drive the Market's Growth
- Automobiles are an essential part of human lives as the main mode of transportation today. Currently, there are over 1.3 billion motor vehicles on the road globally, with that number expected to rise to 1.8 billion by the year 2035. Passenger cars comprise roughly 74% of these statistics, while light commercial vehicles and heavy trucks, buses, coaches, and minibusses make up the remaining 26%.
- 3D printing can be used in making molds and thermoforming tools for the rapid manufacturing of grips, jigs, and fixtures. This allows automakers to produce samples and tools at low costs and eliminate future production losses when investing in high-cost tooling. The first-ever 3D-printed electric car was launched in 2014 by Local Motors. Subsequently, other established firms, like the BMW group, have also followed suit in terms of adopting automated 3D printing techniques. In several major US auto manufacturers, around 80%-90% of each initial prototype assembly has been 3D printed, with an increasing trend toward automation. Some of the popular components are parts of the exhaust, air intake, and ducting. These parts are designed digitally, 3D printed, and fitted on a car in short order, then tested through multiple iterations.
- Perhaps the most popular use of automated 3D printing in the automotive space is fabricating manufacturing aids like jigs and fixtures. Making manufacturing tools using traditional means is rather costly and time-consuming, and geometry limitations translate into less efficient manufacturing processes and more constraints on the geometry of end-use parts. Manufacturing tools that are 3D printed are lighter and more ergonomic, making it easier and safer for factory workers to perform their duties.
- Furthermore, the production volumes associated with automotive manufacturing are very high, tallying to hundreds of thousands of runs for every part. That would be difficult for most 3D printing technologies to keep up with (for now). But many high-end automobile manufacturers limit the production runs of their cars to only a few thousand units, which makes automated 3d printing a viable option.
- According to the World Economic Forum, more than 12 million fully autonomous cars are expected to be sold per year-on-year 2035, covering 25% of the global automotive market. Also, several initiatives taken by the electric motor manufacturers are leading to the growth of the market. In March 2020, UK-based engineering company Equipmake developed a power-dense permanent magnet electric motor. The motor was designed in collaboration with Hieta, a 3D printing specialist. Equipmake's Ampere motor will weigh near to 10kg but provide an output of 295bhp.
- Furthermore, Brackets are small and rather mundane parts, which were very difficult to optimize in the past time when engineers were constrained by the traditional manufacturing methods. Currently, engineers can design optimized brackets and bring these designs to life with the help of 3D printing. Rolls Royce recently showcased the capabilities of 3D printing for brackets. The company showed off a large batch of DfAM-optimized and 3D-printed automotive metal parts, many of which look to be bracketed. While prototyping remains the primary application of 3D printing within the automotive industry, using the technology for tooling is rapidly catching on. One major example of this is Volkswagen, which has been using 3D printing in-house for a number of years. Their binder jetting technology is also in use to construct the component. Also, in July 2021, Volkswagen stated that it is partnering with Siemens and HP to industrialize 3D printing of structural parts, which can be significantly lighter than equivalent components made of sheet steel.
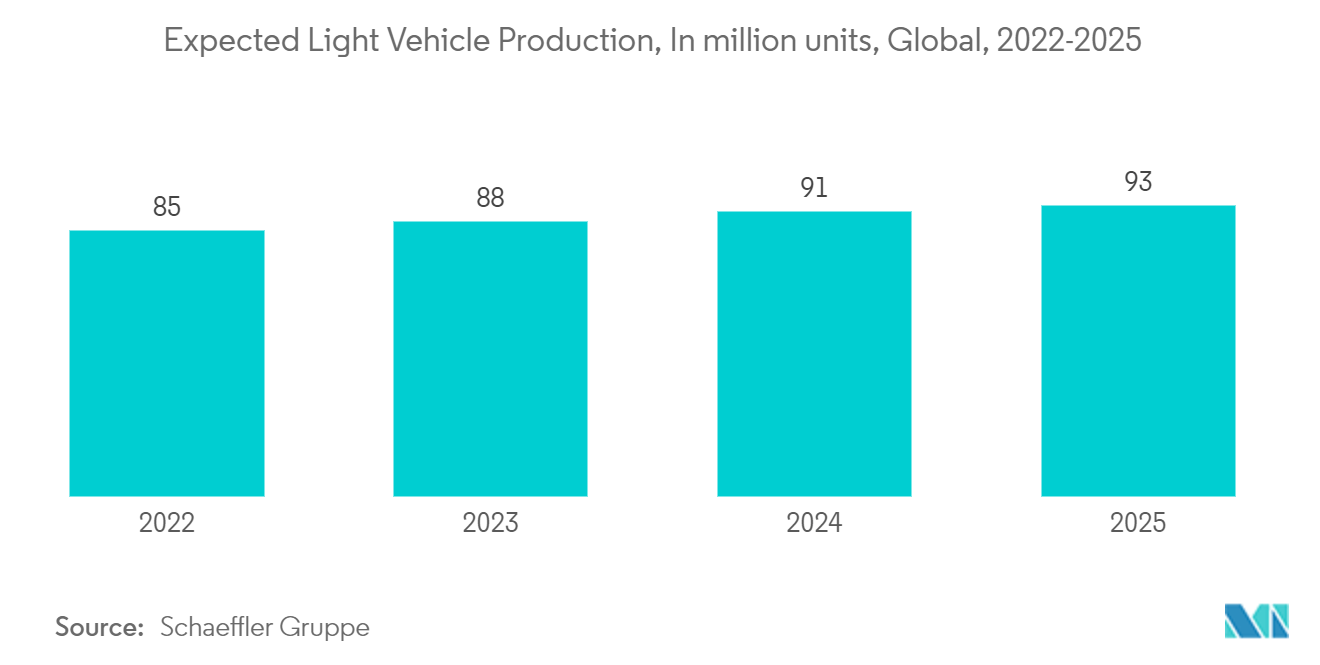
North America is Expected to Hold a Major Market Share
- North America is one of the significant markets for Automated 3D printing globally, with the United States accounting for a significant share in the region. The country's rising demand can be attributed to the vast presence of small and big vendors. For instance, Forecast 3D in Carlsbad, CA, offers 3D printing services in a variety of materials to the healthcare, automotive, aerospace, consumer products, and design industries.
- Closed-loop control systems have long been a fundamental aim for additive manufacturing engineers due to the rapid development of powerful AI applications. For instance, Researchers at GE's Niskayuna Additive Research Lab, New York, created a proprietary machine-learning platform that uses high-resolution cameras to monitor the printing process layer by layer and detect streaks, pits, holes, and other problems that are typically invisible to the naked eye. Further, The data is compared in real-time to a pre-recorded flaws database utilizing computer tomography (CT) imaging. The AI system will be trained to forecast difficulties and detect flaws throughout the printing process using the high-resolution image and CT scan data.
- Furthermore, the market is witnessed with various technology patents for polymer 3D printing. For instance, in August 2020, PostProcess Technologies Inc., one of the providers of automated and intelligent post-printing solutions for industrial 3D printing, received a patent for automated post-printing technology for polymer 3D printing. The SVC technology is part of PostProcess's additive manufacturing family of 3D printed polymer support removal and resin removal solutions. This patented method uses patent-pending detergents and proprietary algorithms to ensure that 3D printed components are exposed to detergent and cavitation uniformly, consistently, and reliably during post-printing.
- Also, various vendors are expanding facilities into the region, primarily to address the supply chain challenges and growing demand in various end-user verticals. For instance, in February 2021, Roboze announced the opening of its US headquarters in Houston, Texas, to facilitate the reshoring of domestic production and address supply chain issues. Roboze will be able to increase its engineering and production capacity in the United States with plans to hire over 100 employees in the next two years and address a growing demand for 3D printing technology in industries such as aerospace, oil and gas, and mobility.
- Similarly, in April 2021, Roboze announced the launch of Roboze Automate, the industrial automation system to bring customized 3D printing with super polymers and composites into the production workflow for extreme end-user applications. The United States is experiencing a metals deficit that is affecting each of the industry areas as it begins an infrastructure push that spans from energy to transportation to manufacturing. Roboze combined its novel polymer platform technology, PEEK, an ideal metals replacement technology, with a PLC industrial automation system developed in partnership with B&R.
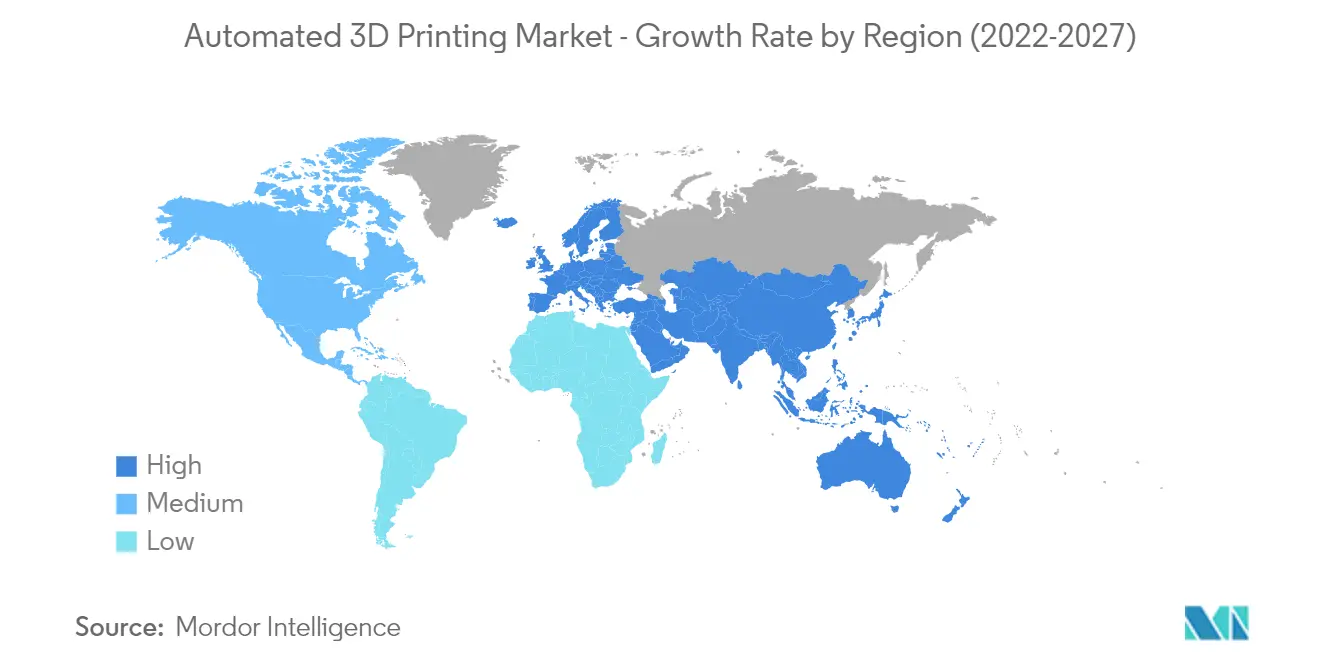