Market Trends of Australia & New Zealand Water Treatment Chemicals Industry
Municipal End-user Industry to Dominate the Market
- Ensuring a consistent supply of pure water to households remains a top priority for governments worldwide. In Australia and New Zealand, the scarcity of potable water, driven by a growing population and demand, is boosting the water treatment chemicals market.
- There are 140 types of chemical contaminants, with chlorine, ozone, potassium permanganate, and copper sulfate being the most commonly used to remove pollutants from wastewater.
- Australia, with a population of 26 million, has 94% of its residents linked to the primary water supply. The nation has about 300 urban water utilities, with 22 serving 70% of the populace, while the smallest 200 serve 13%, a figure eclipsed by Sydney Water, Australia's largest utility.
- Data from the South Australian government shows Adelaide has three main wastewater treatment facilities: Bolivar, Glenelg, and Christies Beach. There is also a smaller plant at Aldinga and 20 more across the Adelaide Hills and regional zones. In 2023, the government allocated AUD 534 million (USD 351 million) to renew sewerage assets and expand the system for future growth.
- Currently, 85% of the population has access to over 700 community sewage treatment facilities. Nearly half use biological filters, around 170 are lagoon-based, and 45 use primary treatment methods. Most new plants are adopting activated sludge processes.
- Recent treatment plant expansions in Australia and New Zealand are driving demand for water treatment chemicals. In December 2023, North East Water began a significant upgrade to Wodonga’s wastewater treatment facility, supporting population and business growth alongside environmental outcomes. This AUD 73 million (USD 48 million) project is slated for completion by the end of 2025.
- In January 2024, an AUD 238.5 million (USD 156.8 million) enhancement began at Woodman Point Water Resource Recovery Facility in Munster, Western Australia’s largest wastewater treatment plant. This facility processes 150 million liters of wastewater daily, serving 900,000 homes and businesses in Perth’s southern suburbs. The upgrade sets a new standard in sustainably transforming wastewater into clean water, renewable energy, and other resources.
- The above-mentioned factors are expected to fuel the demand for water treatment chemicals from the municipal segment in Australia and New Zealand during the forecast period.
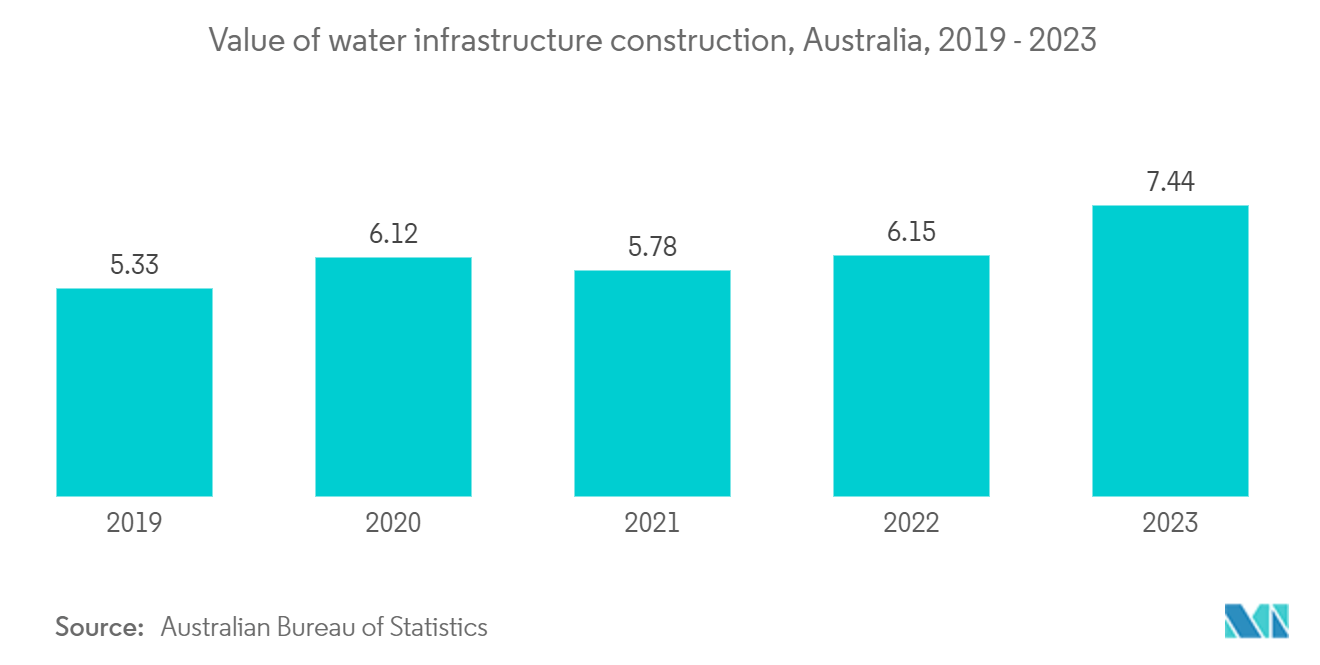
Corrosion and Scale Inhibitors to Dominate the Market
- Corrosion inhibitors are essential chemicals used to combat corrosion in boilers. Corrosion arises when oxygen interacts with a boiler's metallic components, forming oxides. This impacts the boiler's parts and increases energy and maintenance costs. Corrosion inhibitors form a thin barrier layer to protect exposed components. Scale inhibitors use chemical processes to eliminate scales.
- Water boilers employ various corrosion inhibitors, including condensate line corrosion inhibitors, diethyl hydroxyl amine (DEHA), polyamine, morpholine, cyclohexylamine, and carbon dioxide corrosion inhibitors. Condensate line inhibitors, made from filming amines, protect across high and low vapor/liquid scenarios.
- DEHA acts as an oxygen scavenger and metal passivating agent. Polyamine suits both low and high-pressure boilers. Morpholine raises the liquid's pH level for protection. Cyclohexylamine is used in low-pressure boilers, while carbon dioxide inhibitors, paired with polyamine, manage corrosion.
- These inhibitors are crucial in cooling water treatments, safeguarding metals, and preventing losses. Without them, failures could arise in recirculating water piping, process cooling equipment, and heat exchangers. Corrosion inhibitors reduce the corrosion potential at the cathode and anode of the corrosion cell.
- Cooling water treatment systems, especially those with steel and copper alloys, face severe corrosion. Water treatment involves processes like pretreatment, coagulation, flocculation, and corrosion control, with inhibitors added post-filtration to prevent fouling. Corrosion inhibitors extend the service life of piping in water distribution systems.
- In the oil and gas sector, corrosion inhibitors are pivotal. They form the backbone of asset integrity programs, reducing equipment failure rates. They protect wells, pipelines, tanks, compressors, and other equipment. The industry would face setbacks without these inhibitors.
- As various end-user industries seek solutions to mitigate corrosion during processing, the demand for corrosion inhibitors grows, driving market growth.
- Calcium and magnesium chemicals in water form carbonates and bicarbonates, which deposit on boiler surfaces as scales. These scales hinder heat transfer, induce localized heating, and increase power consumption and maintenance costs.
- The oil, gas, and petrochemical industries, major consumers of scale inhibitors, are recovering, signaling potential market impacts.
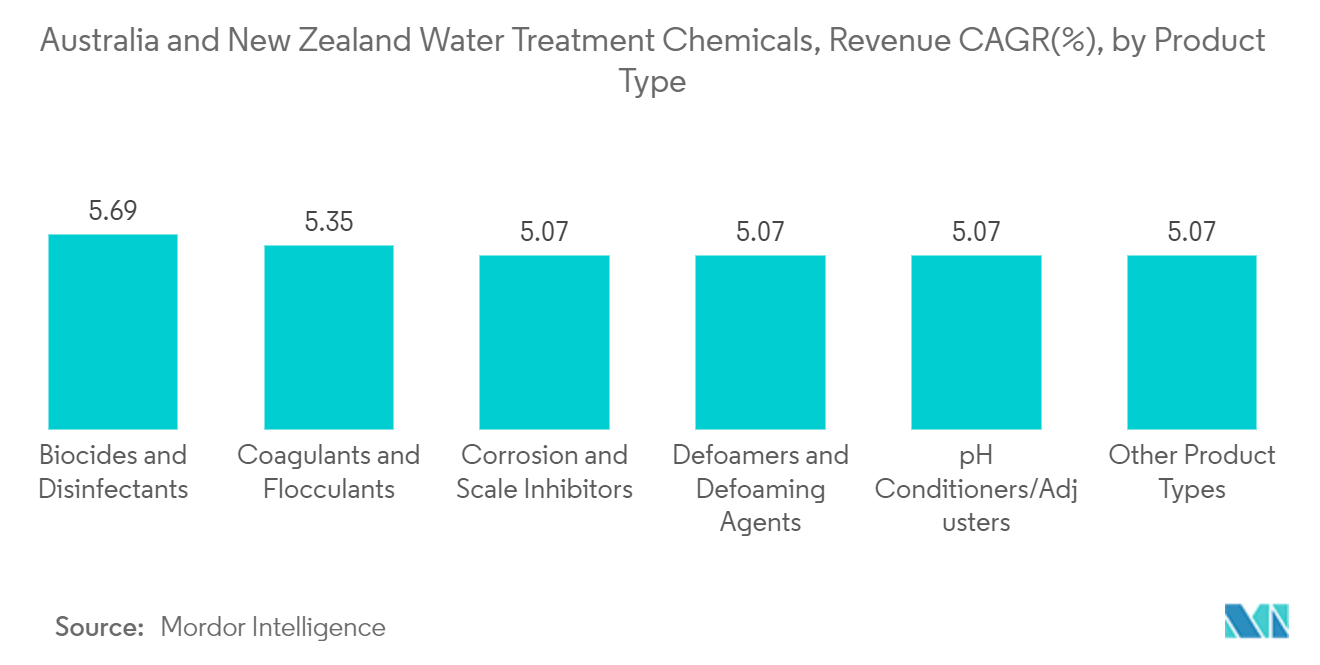