Market Trends of Asia Pacific Automotive Bearing Industry
There Is Growing Demand for Rolling Element Bearing
- The current investment in the plant and machinery by Indian forging companies is worth INR 27,83.3 billion (USD 378.40 billion). The industry is increasingly addressing opportunities arising out of the growing trend among global automotive OEMs to outsource components from manufacturers in low-cost countries.
- The auto sector currently accounts for approximately 58% of overall forging production, with the remainder going to the non-auto sector. Because forging components are the backbone of the Indian automobile industry, changes in the Indian automobile industry have a direct impact on the Indian forging industry. Because the automobile industry is the primary customer for forgings, the industry's continuous efforts in upgrading technologies and diversifying its product range have enabled it to expand its customer base to foreign markets.
- Significant demand for automobiles also led to the emergence of more original equipment and auto components manufacturers. As a result, India developed expertise in automobiles and auto components, which helped boost the demand for Indian die-casted auto components, propelling the market growth.
- As per the Automobile Component Manufacturers Association (ACMA) forecast, auto component exports from India is expected to reach US$ 30 Billion by 2026. The auto component industry is projected to record USD 200 Billion in revenue by 2026.
- As a consequence of this high demand from some of the large automotive markets of Asia-Pacific, the demand for rolling element bearing is anticipated to increase in the coming years.
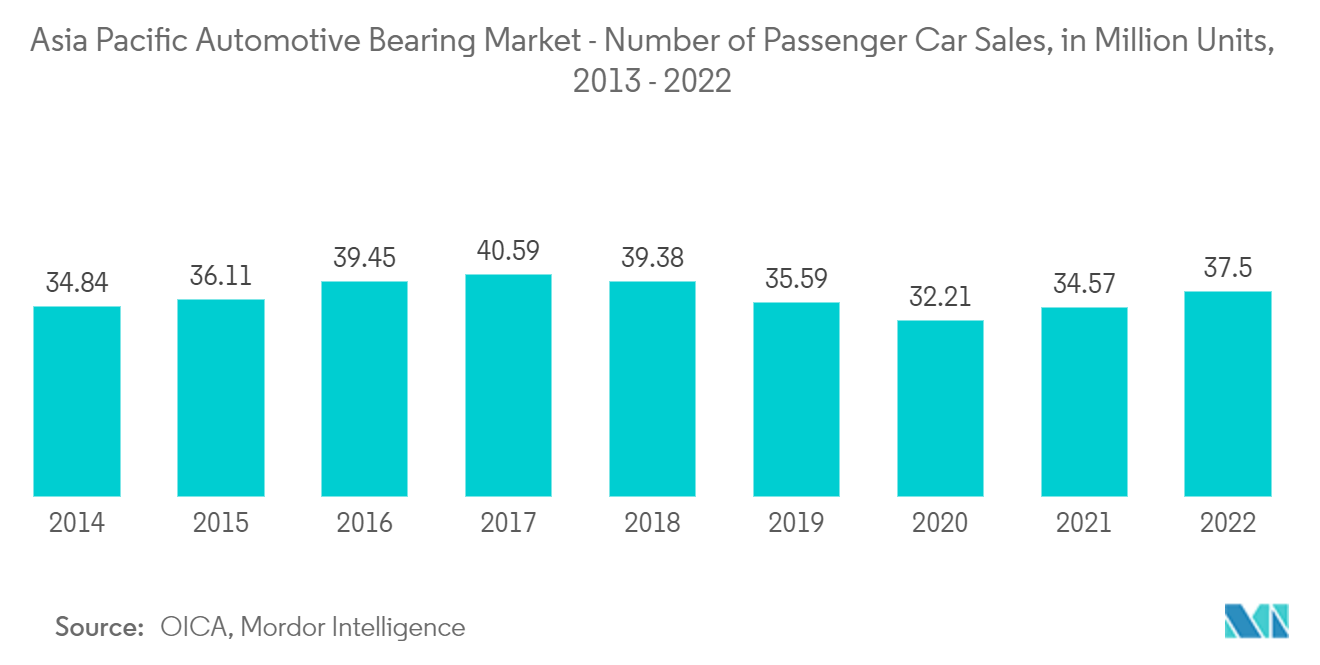
China likely to lead the Global Automotive Bearing Market
- China is one of the largest markets for automobiles in the world and is expected to grow more in the future. An increase in the production of passenger cars and commercial vehicles is expected to drive the market for automotive parts developed through aluminum die casting. Pollution is becoming a serious concern, and governing bodies are focused on curbing the pollution caused by vehicles. At the same time, automobile manufacturers are opting for lightweight components to reduce fuel consumption and curb the emission of harmful pollutants into the atmosphere.
- The government is pushing automobile manufacturers and encouraging customers to adopt electric vehicles by providing subsidies as the country is planning to completely ban diesel and petrol vehicles. An increase in the production of electric vehicles, such as passenger cars and commercial vehicles, is expected to boost the sales of automotive parts developed through die casting.
- The rise in demand for electric and hybrid vehicles turned the focus of automotive manufacturers toward using lightweight materials like aluminum as a substitute for heavier steel and iron in all types of vehicles. According to some estimates, the average aluminum content used in 2021 to manufacture a battery-electric vehicle in China was 173.1 kg per vehicle. Now due to advancements in technology, aluminum's inhered strength, and significant weight reduction properties, the usage of aluminum is expected to increase by up to 70% by 2027. Similarly, in 2021, the average aluminum used in electric commercial buses was around 244.5 kg, which is expected to reach 340.6 kg by 2027, indicating an increase of more than 70% in the use of aluminum in manufacturing.
- Thus, the application and demand for aluminum parts are predicted to increase in the Chinese automotive industry. This, in turn, would expand the market for aluminum die casting in the Chinese automotive industry. Key players in the market are expanding their production capacity to cater to the increased demand for automotive parts and aluminum die casting. For instance,
- In March 2022, Linamar Corporation signed an agreement with Binhai New Area, Tianjin, to manufacture Skyjack products in China for the Asia-Pacific market. In March 2022, Georg Fischer Casting Solutions, a subsidiary of GF Group, announced that the construction of its new plant in Shenyang, China, is progressing according to the schedule, and production was started by the end of 2022.
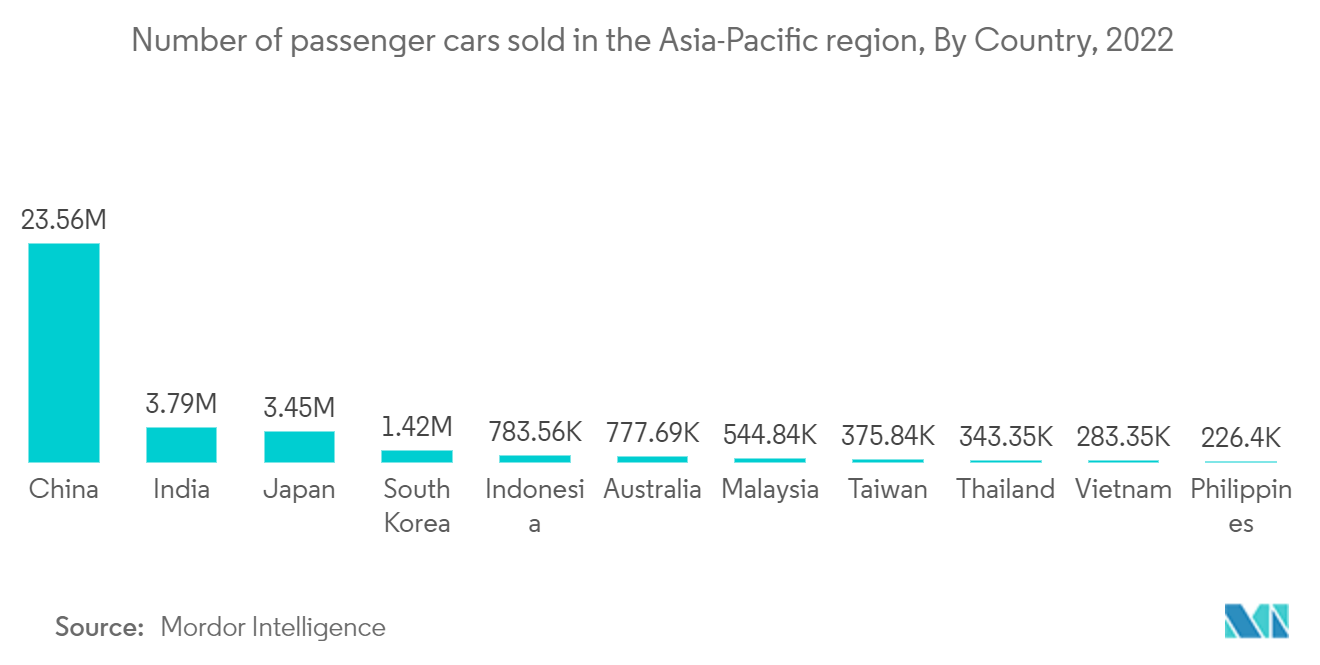